Severn understands the ongoing challenges operators face with reducing and eliminating fugitive emissions and have created a technical solution with the design of its Oblique Cone Technology Triple Offset Butterfly Valve.
Operators are under increasing pressure to reduce fugitive emissions for both onshore and offshore assets in order to achieve their core imperatives of safe operations and minimum downtime. Severn realises the role they play in today’s climate conscious world to help reduce and eliminate fugitive emissions from valves. Utilising the engineering heritage and extensive knowledge in severe service applications, Severn ensures it can offer the most suitable product for the end user.
Through Severn’s ‘Repair Intelligence’ and close operating relationships with end user operators, Severn has been able to understand the difficulties facing operations in the specification, purchasing and servicing of Control, Choke and Butterfly valves that are critical to reducing fugitive emissions across industrial facilities. Severn prides itself in offering technical solutions that perform no matter how severe or critical the application is. Ensuring that the end user gains the best valve performance and reduced maintenance costs over the lifecycle of the valve.
It has long been understood that approximately 60% of fugitive emissions come from valves. Even more so 80% of those emissions are related to the stem/shaft seal. Naturally, the focus is on this area with the relative fugitive emissions standards such as API 622 and ISO 15848. What is often misunderstood is the requirement for the standards to be applicable across varying temperature and pressure differentials. For this reason, Severn has 43 different certificates for sealing systems in valves based on their application requirements, up to 10,000 Psi and 425ºC. By utilising a range of materials from filled graphite through to custom PTEE-based compounds, Severn has, coupled with novel packing designs, been able to achieve tighter leakage rates that had previously been achieved with standard packing sets.
It is vital for the end user to understand the leakage class requirements when fugitive emissions are concerned to prevent over or underspecifying the solution. We often see “fugitive emissions” specified without clarification of the requirements. The various requirements from TUV through API and ISO specifications require different testing methodologies and even different testing mediums. This means that the testing standards are not directly comparable to each other. Severn often see the specification of “Low-e” or “Low emission” packing without reference to the specification. In some instances, these packing sets can have allowable leakage of up to 500ppm, many times that of systems tested to the ISO 15848-1 standard and potentially resulting in detrimental reduced on-site performance and / or higher maintenance costs.
Severn has focused and will continue to focus its testing efforts on ISO 15848 standards as it is understood that these offer the widest range of qualification options whilst not utilising harmful greenhouse gases that can be emitted using some API methodology. The fact that sealing systems are tested on the valves they are designed for and not a standard test fixture ensures maximum customer confidence in our products performance and reliability.
Severn have focused on passing some of the most stringent testing with class A leakage classes and up to 40,000 operations available for some applications. Ensuring that performance is at the heart of our product range, and you achieve your core remit of safe operations and minimum downtime.
To further the commitment to reducing fugitive emissions and reduce the burden on end users to meet tightening specifications, Severns OCT Triple Offset Butterfly Valve offers the fugitive emissions packing sets as standard fitment on all standard valves in the range. Ensuring that the end user experiences maximum valve performance in all applications.
Severn’s engineering heritage and technical expertise have led to the OCT TOV Butterfly Valve being future-proof for changes in the process conditions to provide increased versatility for the end user.
From the outset, Severn made flexibility a key driving force in the design of the Oblique Cone Technology (OCT) Triple Offset (TOV) Butterfly Valve. Due to Severns extensive diverse engineering heritage and excellence, our expert team of engineers understand that processes and application product demands change over time, whether it is the process conditions or the overall requirements of the valve for the end user. Due to this understanding, the Oblique Cone Technology Triple Offset Butterfly Valve has been designed to incorporate multiple seal options, all fully interchangeable with each other, providing maximum application diversity and usability to ensure safe operations and minimum downtime.
The Laminate seal is the “traditional” Triple Offset Valve seal and consists of multiple metal and graphite layers providing isolation sealing.
The OCT HS seal is a hybrid polymer metallic seal, this seal benefits from a primary metal seal and secondary polymer seal, this provides a reliable and repeatable bubble tight seal time after time. This can also be paired with PTFE packings when graphite being in contact with the line media is a concern. The polymer seal is fully compliant with EN ISO 80079-36 (ATEX).
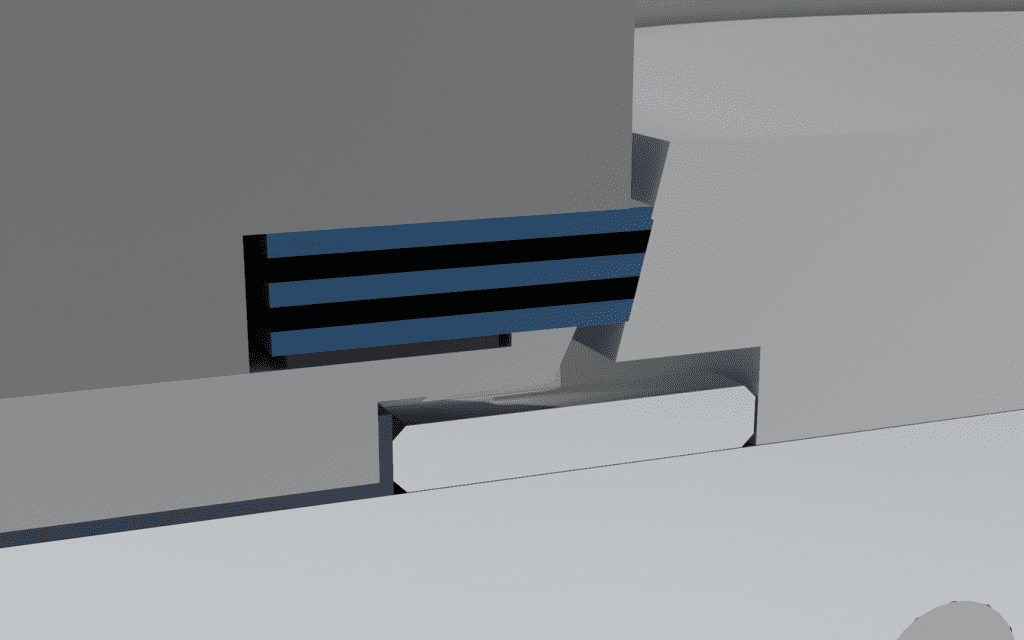
The OCT SW Valve takes the hybrid sealing to the next level with its versatile high performance. Severn utilises the OCT-HS seal and has designed a valve that ensure there is no graphite in contact with the line media to remove the risk of costly galvanic effects such as internal corrosion leading to valve failure. Whilst doing so the OCT-SW also maintains firesafe certification.
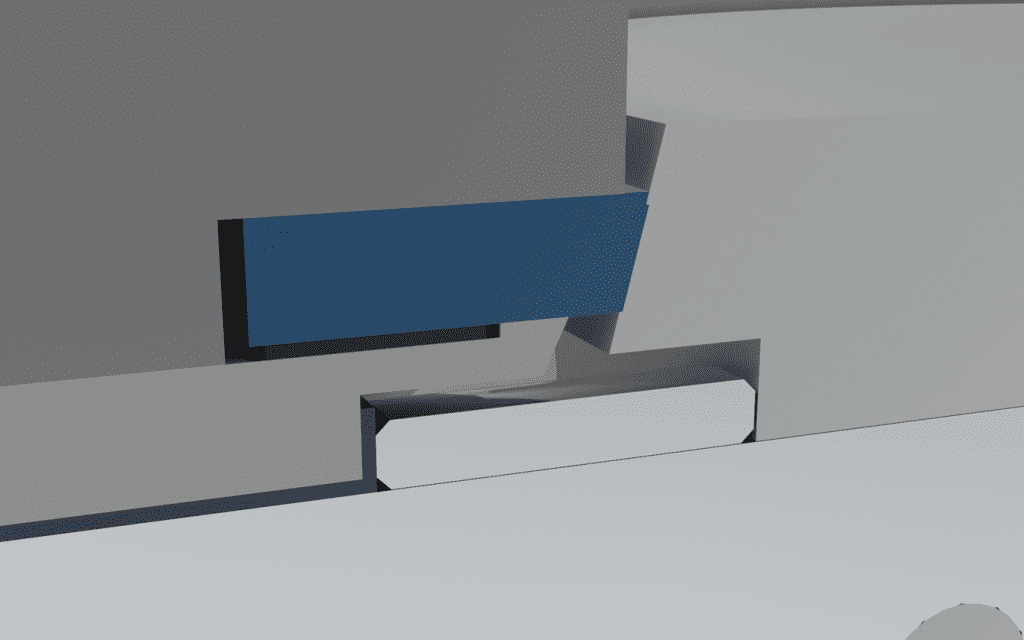
Should the sealing requirement not become as critical, and process conditions become more arduous, the Laminate and Hybrid seals can be changed for the OCT-SS solid seal. As the name suggests it is a solid metallic seal, that can be made from hard-wearing alloys to add longevity to the sealing life of the valve in arduous conditions and can offer a control valve seat leakage.
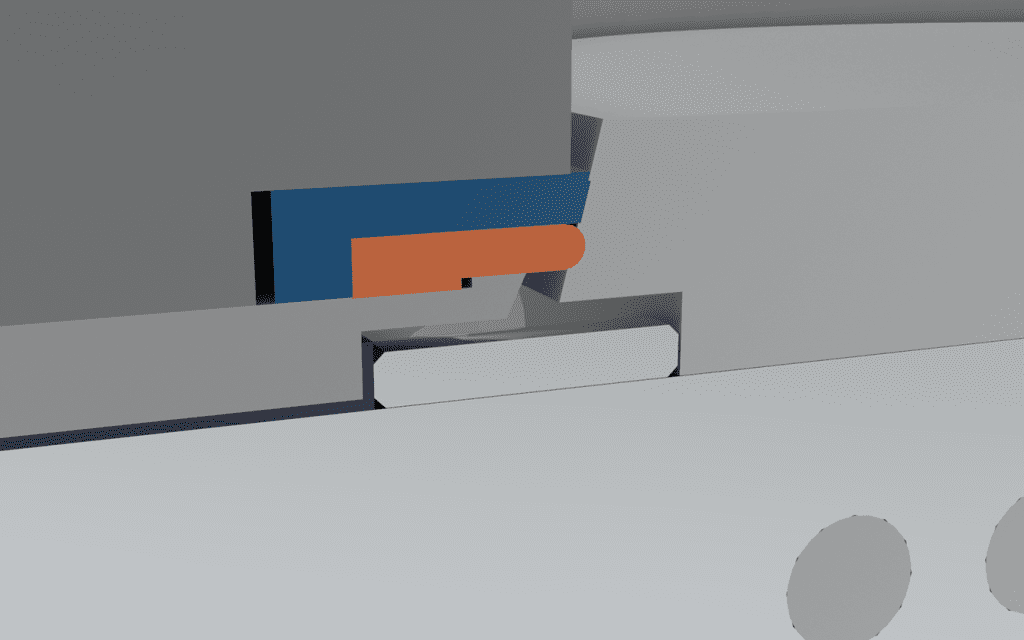
Based on Severns comprehensive history of severe service control, our team of engineering experts work closely with operators and end uses to identify the correct seal and material selection to provide the maximum reliability and productivity further ensuring minimum downtime.
All the OCT seals are interchangeable and can be upgraded without the need for main valve components being replaced, further emphasising the OCT TOV Butterfly Valves versatility. The fully in field serviceable valve can be upgraded on-site without the need for specialist tools or knowledge, this further ensures that costly unplanned downtime and site waste is kept to a minimum, along with potential loss in production for the end user. All the seal options can be changed on site within a small space of time to ensure site maintenance costs are reduced by upgrading the existing valve rather than discarding and replacing with a commodity product each time.
Each OCT valve is specially designed to be versatile and ensure it has multiple purposes for multiple conditions whilst still delivering maximum performance. With the introduction of the interchangeable seal, these can be easily swapped out to match the end users’ requirements, should they change.
The Triple Offset Butterfly Valve Cutting Edge Design Features Leads to Comprehensive Application Coverage.
Incorporating over 60 years of engineering excellence and technical expertise in valve engineering and application, Severn offers an industry leading and patented engineering technology solution(s) for Butterfly Valve requirements and applications with the Oblique Cone Technology (OCT) Triple Offset (TOV) Butterfly Valve. By utilising Severn’s ‘Repair Intelligence’ knowledge which involves providing real market feedback from extensive in-depth analysis from failed valves. Severn have designed each facet of the OCT TOV Butterfly Valve to provide the most accurate, reliable, and robust service capability and performance possible to help the end user achieve their core remit of safe operations and minimum downtime.
Severn’s OCT design uses circular sealing geometry, unlike traditional triple offset designs that use an ellipse. The benefit of circular geometry is that it provides a uniform sealing load around the circumference of the sealing diameter, providing a reliable and repeatable shut-off. By using circles rather than ellipses, it allows Severn to use proven circular sealing knowledge and incorporate this into the TOV Butterfly Valve.
In addition, to this we can also add specialised flow control trims that are traditionally found on double offset valves. These control trims include Anti Cavitation / Low noise, half baffle & full baffles. We can also add special features such as steam jacket and purge ports should they be required, onto our Triple Offset design.
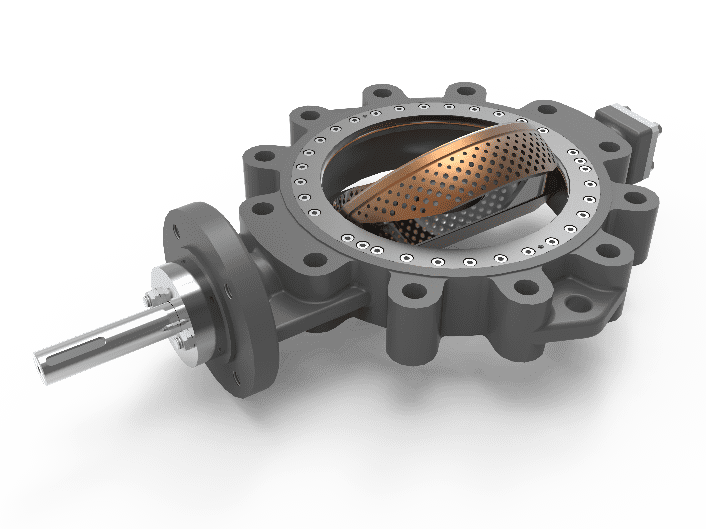
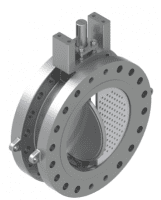

Process conditions can change with time. Severn have ensured the interchangeability of the seal, should the sealing requirement not become as critical, or process conditions become more arduous. The HS seal can be changed to a laminated seal, or if conditions dictate, a solid seal. This can be done without the need for main valve components being replaced. The complete in-field serviceable valve can be upgraded on site without the need for specialist tools or knowledge ensuring possible down time and loss in production is kept to a minimum.
The interchangeability and versatility of the seal allows for Severn’s Triple Offset Valve to be used for both isolation and control applications and processes. The diversity of the OCT TOV Butterfly Valve and its functional usability for an extensive range of both isolation and control applications leads to the potential savings in stock holdings for end users who can use stock this one valve instead of stocking two. This in turn allows for potential cost savings for the end user on stock holding by reducing the need to stock multiple valves due to the extensive coverage that the OCT TOV Butterfly Valve offers.
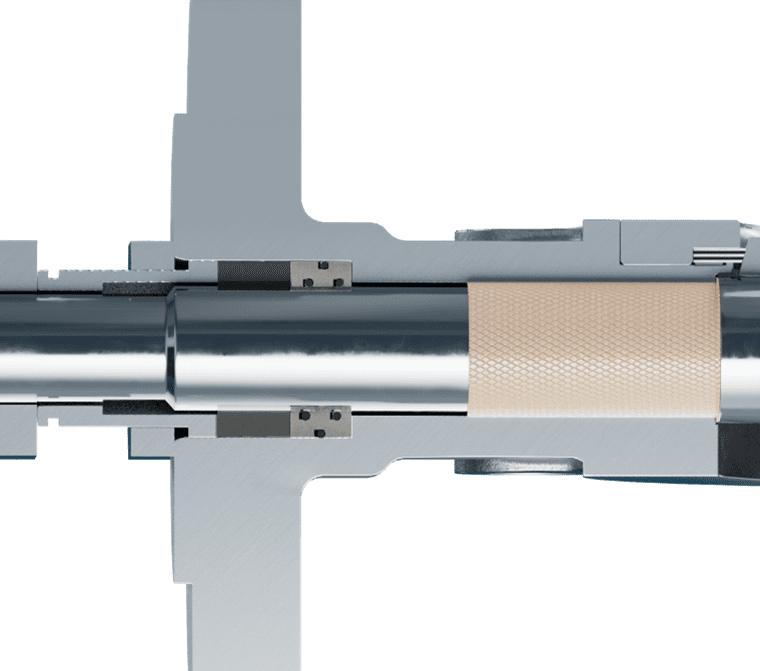
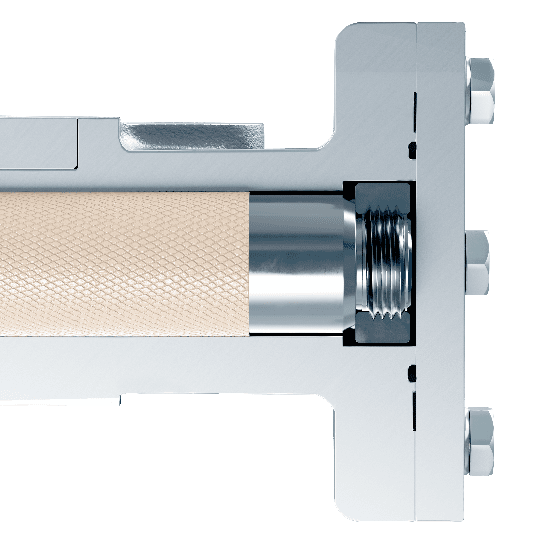
Severn have designed all their Triple Offset Butterfly Valves with safety as paramount and therefore engineered the product with anti-blowout at both ends of the valve. This negates any chance of the shaft blowing out. The reduced shaft diameter at the drive end ensures the shaft cannot blow out through the packing follower and anti-blowout ring on the threaded shaft end ensures positive engagement without the need for additional fasteners.
The OCT range also comes with hard facing on the disc as standard with options to upgrade the standard hard facing to weld overlays such as stellite 6, ensuring and reliable seal and extended service life.
A quarter turn design ensures ease of actuation for both control and isolation purposes. Whether this be via an actuator or gearbox, the quarter turn design allows for simple operation.
As standard, Severn’s OCT TOV Butterfly Valve includes fugitive emission packing to ISO 15848 with options to change to meet customer specific requirements such as Shell 77/312 available.
The OCT valve range has been firesafe tested & certified in accordance with the strict fire test specifications set out in the standards ISO 10497, API 607 & API 6FA. Withstanding extreme temperatures of up to 1000°C whilst still sealing. Further underpinning the performance capabilities and validating the valve performance, ensuring this valve can be suitable for an extended range of applications and process requirements, leading to safe operations and reduction unplanned downtime for the end user.
Severn offer the OCT TOV Butterfly Valve in all cast materials. From basic carbon steels to specialist alloys such as Monel, Titanium & Hastelloy. Severn can provide the correct material selection for your application. Additional surface coatings such as stellite, armoloy, chrome or weld overlays are available upon application and request.
Severn are breaking tradition with the innovative OCT Butterfly Valve and lifecycle enhancement service.
In the fast-paced industrial landscape, the emphasis on sustainability and cost-effectiveness has never been greater. Severn’s Oblique Cone Technology (OCT) Triple Offset (TOV) Butterfly Valve is at the forefront of a new era in valve technology, where the focus shifts from immediate replacements to intelligent lifecycle enhancement and repair strategies. This paradigm shift not only promotes sustainable valve maintenance but also ensures safe operations, reduced downtime, helping you achieve your core remits.
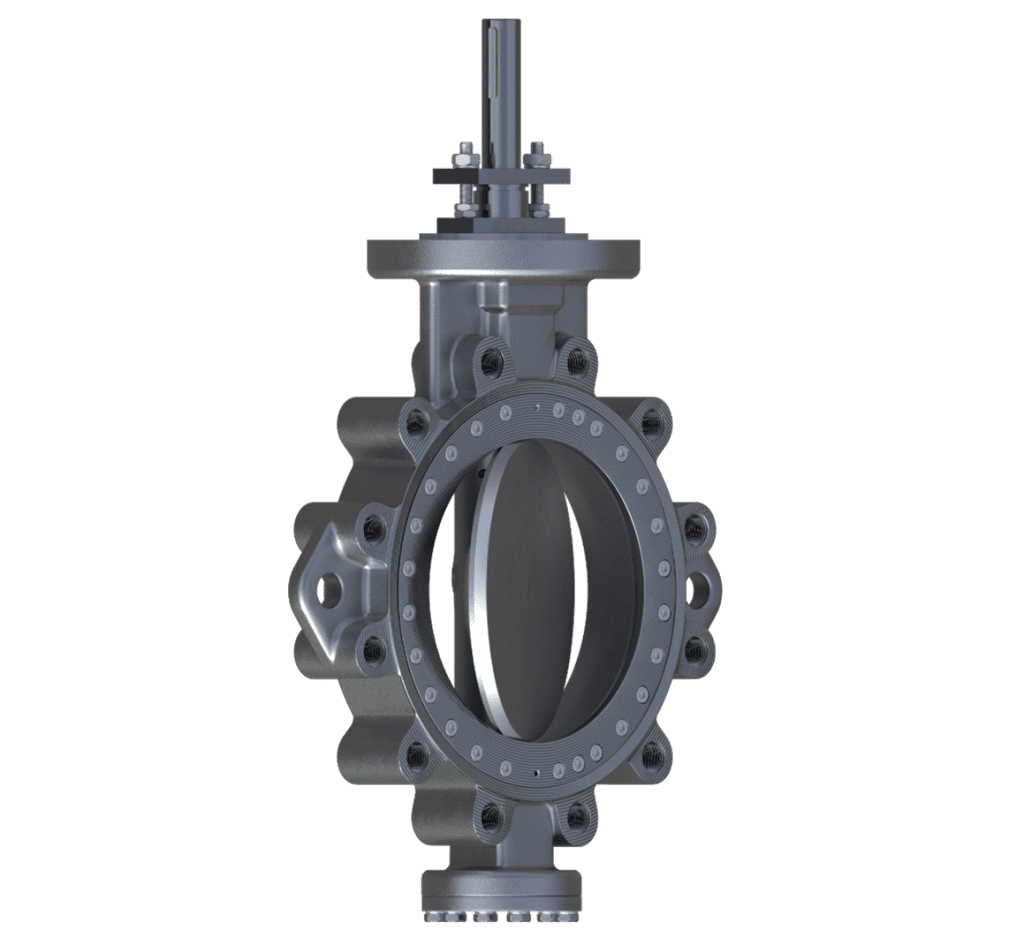
Lifecycle Enhancement: Prolonging Valve Longevity
The traditional approach to valve maintenance often involves a “replace-first” mentality. However, Severn’s OCT TOV Butterfly Valve challenges this norm by offering a comprehensive lifecycle enhancement program. Through cutting-edge innovative engineering and materials, the OCT TOV Butterfly Valve is designed to withstand harsh operating conditions, ensuring a longer lifespan with its patented Oblique Cone Technology Triple Offset capabilities for both isolation and control applications.
By prioritizing lifecycle enhancement, industries can optimise their assets, reduce overall operational costs, and minimise the environmental footprint associated with the manufacturing and disposal of new valves.
Repair Intelligence: Smart Solutions for Complex Issues
The OCT TOV Butterfly Valve affirms the concept of Severn’s repair intelligence as the valves are designed with modular components, facilitating easy disassembly and reassembly during repairs. This not only reduces maintenance costs but also minimises the need for complete valve replacements, contributing to a more sustainable and cost-effective approach to industrial operations.
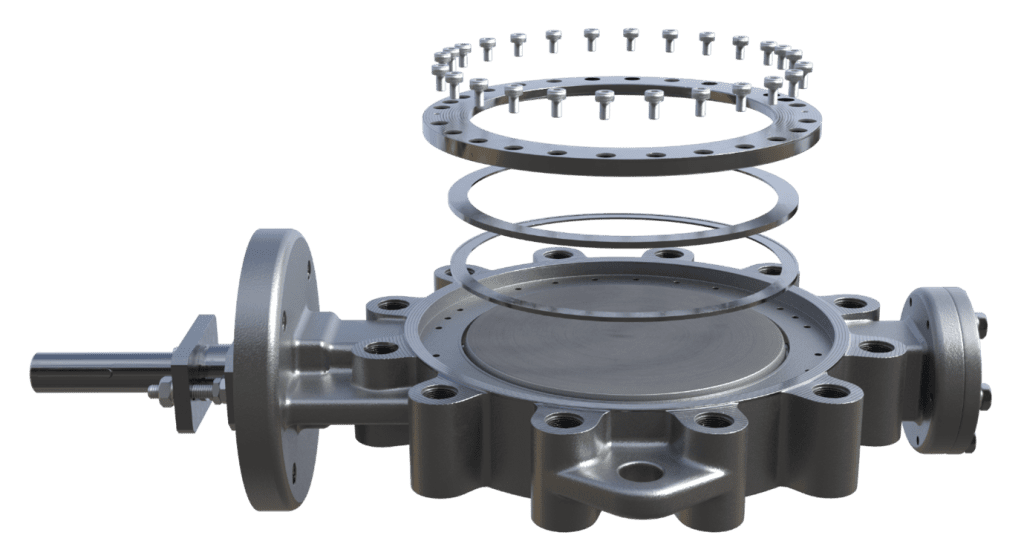
Sustainable Valve Maintenance: A Green Approach
Severn’s commitment to sustainability goes beyond the valve’s design. The OCT TOV Butterfly Valve promotes a circular economy by encouraging refurbishment and reconditioning of components. With our expert team of service engineers based globally, we can retrofit, service and repair any of our Butterfly valves on site if performance has dropped or specification or operating conditions have changed, this ensures production downtime is kept to a minimum.
Furthermore, sustainable valve maintenance aligns with global initiatives to reduce carbon emissions. By extending the life of industrial equipment, companies can decrease their carbon footprint associated with manufacturing and disposal, contributing to a greener and more environmentally responsible future.
Safe Operations and Reduced Downtime: The Ultimate Value Proposition
The OCT TOV Butterfly Valve prioritise safety through rigorous testing and compliance with industry standards such as API 598. By implementing repair intelligence and lifecycle enhancement strategies, Severn can ensure the continued reliability and safety of their valves and valve systems.
Moreover, the ability to address issues proactively minimise unexpected costly downtime. This not only enhances operational efficiency but also safeguards against potential safety hazards, ensuring a secure working environment for personnel.
Environmental Impact: A Positive Footprint for Future Generations
By choosing repair over replacement and embracing Severn’s lifecycle enhancement, industries using Severn’s OCT TOV Butterfly Valve actively contribute to reducing the environmental impact of their operations. Through sustainable valve maintenance practices, companies can align with global environmental goals, demonstrating corporate responsibility and leadership in their respective sectors.
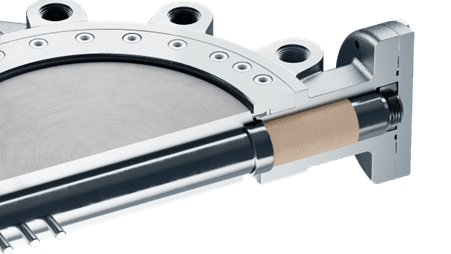
Severn’s OCT TOV Butterfly Valve signifies a paradigm shift in the industrial valve landscape. By championing lifecycle enhancement, repair intelligence, and sustainable valve maintenance, this product offers not just cutting-edge technology but a comprehensive solution for industries seeking a balance between operational efficiency, environmental responsibility, and cost-effectiveness. In a world where every decision impacts the planet, choosing to repair, not replace, is a step towards a more sustainable and resilient future.
Fireproof Assurance: Severn’s OCT TOV Butterfly Valves Exceptional Fire Safety Design and Testing Credentials
As part of a safety-first approach Severn incorporates into its innovative Oblique Cone Technology (OCT) Triple Offset (TOV) Butterfly valve, fire safety is a critical part of that safety first objective. Fire testing standards state the minimum requirements the valve must achieve in order to receive fire safe certification. The standards dictate the setup & parameters required to simulate the conditions a valve may be subjected to during a fire, and test to ensure the valve can operate satisfactorily afterwards.
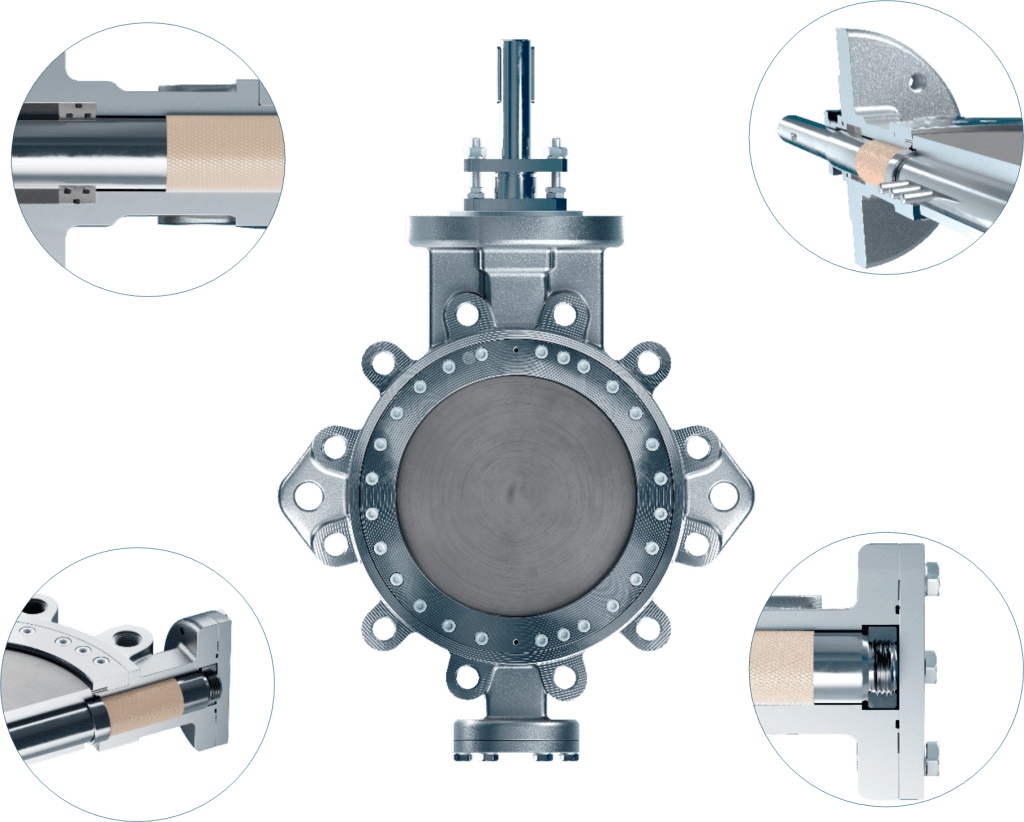
To summarise, the test consists of a valve being mounted in a fire test rig to flow water through the valve, and measure leakage both internally past the seal as well as externally through the packings and gaskets. The valves are then pressure tested at ambient temperature, once the valve has passed this element of the test, any leakage is recorded. The valve is then subject to a simulated fire by use of gas burners, with average temperatures of between 750°C & 1000°C recorded by thermocouples for the 30-minute burn time. Once complete, the flames are extinguished, and the valve is subjected to a forced cooldown using water to simulate the fire being extinguished on site.
The leakage during fire is measured and recorded. The valve is then subject to a re-ambient temperature and operational test, with the maximum leakage requirements being defined within the relevant standard. The tests are carried out in both the preferred and reverse directions and are witnessed by a 3rd party approval body to give added confidence that the valve will perform as required in either flow direction.
By investing in and developing their own on-site fire test facility, Severn can understand and interpret the results to re-design & develop the fire safe valve technology for the OCT TOV Butterfly Valve, to further exceed the requirements set out in the standard. By doing this, Severn have been able to achieve up to Zero seat leakage, even after fire testing, giving further confidence to the capabilities of the valves when installed and further ensuring safety first is achieved for the end user and their operations.
The key to Severn’s success lies in their patented Oblique Cone Technology (OCT), which received approval from the UK Intellectual Property Office in 2018. This innovative design uses an ‘infinite circle’ geometry that allowed the research and development team to develop the circular sealing geometry, which gives the flexibility to use the valve for both isolation and control duties with the option of interchangeable seals and control trims.
Utilising its over 60 years of engineering heritage, Severn have designed and developed the innovative OCT TOV Butterfly Valve, a valve that meets the requirements of API 6FA, API 607, and ISO 10497 fire testing standards. These bi-directional isolation & control valves offer repeatable zero leakage, providing peace of mind for operators while ensuring safety is at the forefront.
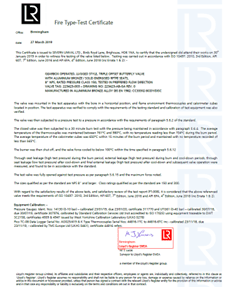
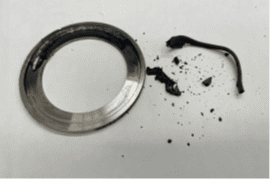
Severn’s certification for fire test covers the OCT Laminate, Hybrid (OCT-HS) and Seawater (OCT-SW) seals, achieving the required leakage rates in accordance with the relevant international standards. By designing, developing, and testing the hybrid seal (OCT-HS) Severn have been able to understand how the hybrid polymer metallic seal acts under extreme temperatures, which has enabled them to develop a graphite free, firesafe seal, that works even after being exposed to the extremes of a fire test. By using this knowledge, the OCT-SW utilises the hybrid seal technology and prevents any graphite from contacting with the line media, therefore on seawater service eliminates galvanic effects and extends the service life of the valve.
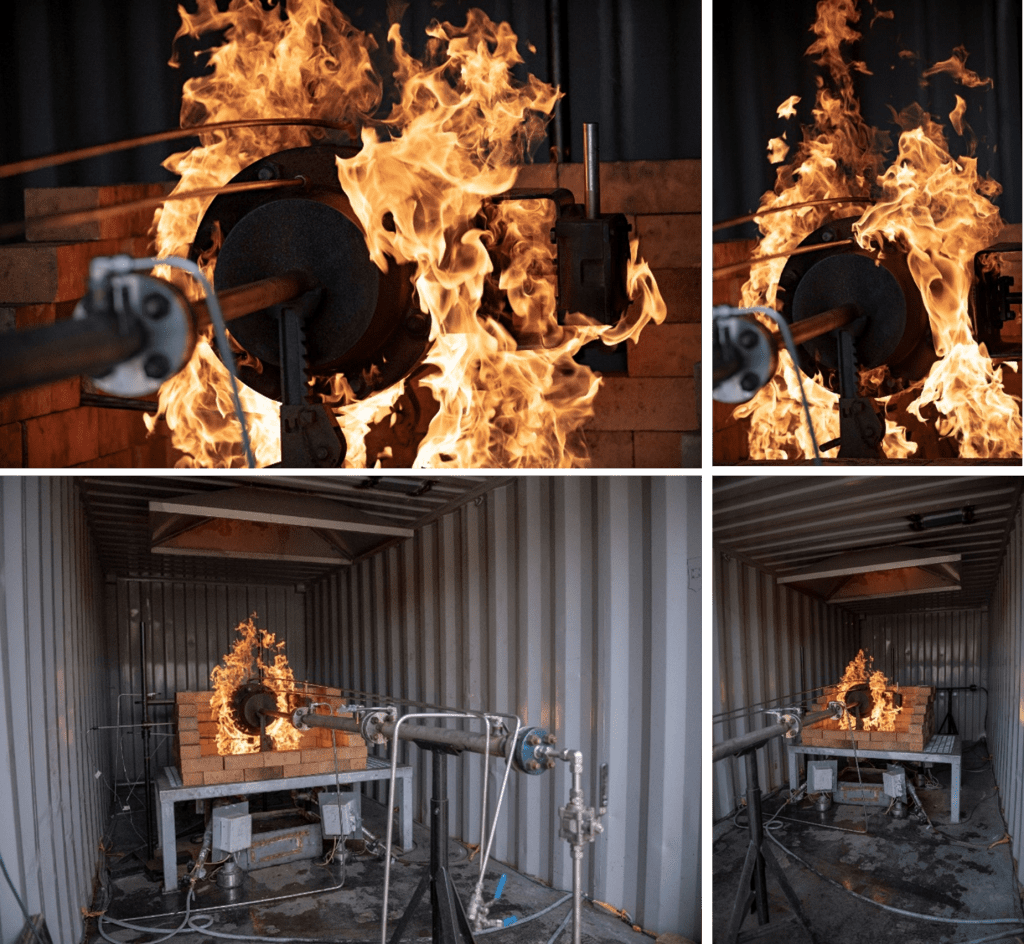
By meeting stringent fire test standards, they have provided customers with a reliable and efficient solution to fire safety. With their patented oblique cone technology, Severn have set a new benchmark for future valve designs and innovative technology and further ensure the end user achieves its core remit of safe operations and reduced downtime.
Exploring the innovative features and engineering principles of Severn’s OCT TOV Butterfly Valve that puts safety first.
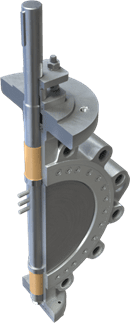
At Severn, safety is paramount in the design of our products. With our background in safety-critical industries, Severn understands the importance of safety first for both our customers and employees.
As well as adhering to the strictest industry standards, Severn have identified that shaft blowout prevention was paramount to our end users and the wider industrial and process industries for improved valve performance and reduced operational downtime.
Butterfly Valve shafts are designed to connect to the disc with either dowel pins, taper pins, or keyways. The separation of the shaft and disc in service can be catastrophically dangerous. If any of these parts fail, the shaft may be ejected from the valve body. Shaft blowouts can occur when a coupling mechanism fails, therefore, disconnecting the shaft from the disc. With the pressures in the system, it may eject the unrestrained drive shaft through either end of the valve.
Not only is this projectile a huge safety concern but has the potential to compromise the pressure envelope of the valve allowing process to escape into the atmosphere.
Severn has designed all their Triple Offset Butterfly Valves as standard with anti-blowout incorporated at both ends of the valve. This negates any chance of the shaft blowing out if the pins were to fail. The reduced shaft diameter at the drive end ensures the shaft cannot blow out through the packing follower.
On the blank end of the valve, Severn have multiple features which prevents shaft blowout. The anti-blowout ring on the threaded shaft end ensures positive engagement without the need for additional fasteners. The blank end plate is locked in place and is designed to withstand full rated test pressures.
Dual anti-blowout devices are standard on the OCT TOV Butterfly Valve, meaning that even if the gland is removed, the secondary internal anti-blowout device will stop ejection of the shaft under the pressure, thus increasing both operator and plant safety.
Severn have designed their Triple Offset Valves to exceed the minimum wall thicknesses stated in ASME B16.34. Instead of just using the minimum allowance, Severn have gone above and beyond to ensure the safety of our products in the field for our customers.
Within Severn’s Triple Offset Butterfly Valve is a corrosion allowance. This means that the valve can afford to concede material to corrosion over time without affecting the pressure containing integrity or safety of the valve. The amount of corrosion may vary depending on the environment the valve is working in, but due to Severn’s engineering heritage and excellence, the OCT TOV Butterfly Valve has been designed to withstand changes in working environments and process conditions.
High MAST figures and safety factors are key when designing the Triple Offset Butterfly Valve. MAST is the Maximum Allowable Shaft Torque a quarter turn valve shaft can withstand during operation without mechanical failure. With Severn using higher MAST figures on their Triple Offset shafts, this helps maintain the structural integrity of the valve.
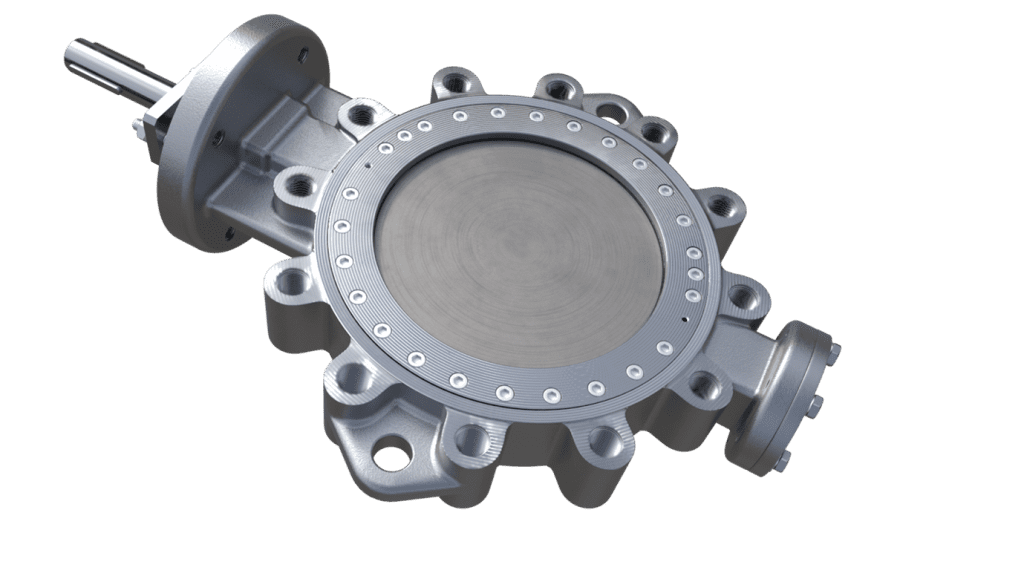
Sizing actuators correctly is a credit to Severn’s engineering excellence. Actuators, gearboxes, or any form of obturator that drives a quarter turn valve must be sized correctly by using the correct input and output torques. By torque testing the physical products prior to final inspection, we can compare the physical torques against our theoretical torques to maintain accuracy and consistency across the range.
Safety has always been at the forefront of Severn’s designs, and this is paramount in the 8500 Butterfly Valve range.
Unveiling the role of Severn’s OCT TOV Butterfly Valve in cavitation mitigation and valve protection.
Severn understands the needs and demands of critical applications and for over 60 years have been pioneering technology development to solve industry needs and provide extended service life of our products. One of the significant issues we see with severe service application valves is cavitation.
Cavitation is only evident in fluid applications and the affects are well understood. However, challenges to offer the most cost-effective solution as opposed to the correct solution, can drive users to selecting sub optimal trims for the application. Users are often expected to understand all the implications of every application(s) to ensure the best valves are selected. At Severn, our industry experts use that knowledge to ensure the best technical solution is offered every time.
Cavitation is a phenomenon that is often seen in valve applications. This can cause dangerous and costly problems to the end user as it only occurs in liquid applications and usually when the flow is being throttled. When cavitation occurs it often creates severe levels of noise and vibration that not only is hazardous to the user but can also cause considerable damage, resulting in costly and unplanned downtime and maintenance. At Severn, we have seen first-hand the effects of cavitation on trims, reducing valve lifetime from years to just weeks, through our ‘Repair Intelligence.’
Cavitation occurs when the fluid in a valve reduces in pressure to a point at which the pressure is below the vapour pressure of the fluid. But what does this mean? If we consider water boiling this is an example of the vapour pressure of a fluid being reached at atmospheric pressure. If we now put the water in a vacuum, then we can make the same fluid boil at a reduced temperature. These pressures and temperatures at which the fluid vapour pressure sits are specific to each fluid type and as such each case must be treated independently.
When a fluid passes through an orifice such as a valve or trim, we see the pressure is inversely proportional to the velocity of the fluid. As the velocity increases through the valve the pressure will decrease.
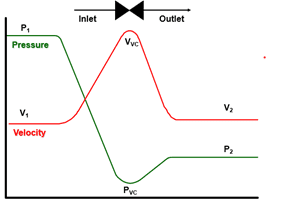
This can, in some circumstances, cause the pressure to fall below that of the vapour pressure of the fluid.
In this instance bubbles will occur in the fluid. When this happens the volume of the fluid can increase but the space inside the valve does not. This leads to the potential of increased velocity through the valve. Should there be entrained solids (such as sand) within the valve then this can have a significant erosion effect on the valve and be a cause for premature wear.
After the fluid has passed through the restriction it recovers in pressure on the other side of the orifice. This recovery in pressure and associated reduction in velocity can cause the fluid to recover above the vapour pressure of the fluid.
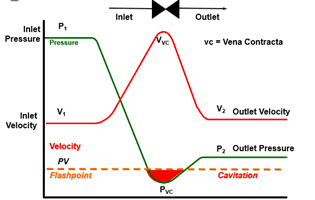
This causes the bubbles previously formed to rapidly collapse producing a shockwave. The forces involved in this are extremely violent. So much so the implosions can tear metal from components creating the characteristic pitting seen with cavitation failure.
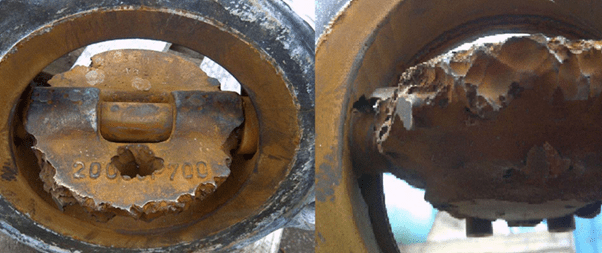
Aside from the physical damage to the valve internals, cavitation can manifest itself as loud noises, often described as “marbles in the pipeline.” These soundwaves create significant vibrations in the valves, pipework, and instrumentation, leading to failures of equipment outside of the valves flow paths due to high vibration and fatigue.
How does Severn’s OCT TOV Butterfly Valve mitigate the effects of cavitation?
By controlling the pressure drop through the valve we can prevent the onset of harmful cavitation. In a Butterfly Valve this often occurs at low openings. At these low openings we often see high velocities between the disc and valve body. Severns patented Oblique Cone Technology (OCT) allows the use of a fully circular disc and with the benefit of a true circle comes the advantage that full anti-cavitation / low noise trims can be fitted where required providing excellent cavitation control whilst still providing reliable shutoff.
In combination with the anti-cavitation disc, the OCT TOV Butterfly Valve can also be fitted with a full or half baffle as required to offer the best solution dependent on the process conditions provided.
At Severn, it is critical that the application knowledge is applied to the valve sizing to ensure the best possible solutions for the end user, ensuring costly unplanned downtime is kept to a minimum whilst achieving safe operations.
Severn’s engineering heritage and excellence has led to the innovative design of a product that can master both Control & Isolation applications.
Utilising Severn’s long history with Control Valve design, our team of engineering experts have been able to manufacture a Triple Offset Butterfly valve that can be used to provide superior control in both throttling and modulating service, whilst additionally providing a repeatable seal for isolation duties.
By designing a Control Valve that can isolate, rather than an isolation valve that controls (which may initially sound the same but is vastly different), Severn have designed a Butterfly Valve that maximises the Cv with streamlined internals to provide optimal flow characteristics when controlling the process.
We have also eliminated the need to have fasteners on the disc or a bolted-on seal, thus enabling us to optimise the disc profile. Additionally, by removing fasteners from the disc, we have eliminated the risk of loose fasteners falling into the line due to vibration.
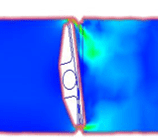

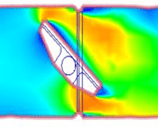
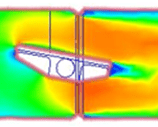
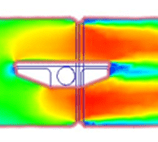
By adopting a body-mounted seal we have been able to increase longevity & reliability of the product. As we have taken this out of the flow path of line media, this reduces wear on the seal allowing Severn to maximise the bore size for an increased CV.
Using our Patented Oblique Cone Technology (OCT), we can also use circular sealing geometry which provides an even seal load around the circumference of the disc. This gives us repeatable bubble-tight sealing, improving product performance, reliability, and safety, ensuring you achieve your core remit of safe operations and minimum downtime.
The OCT geometry enables Severn to add an extensive range of trims to the valve not traditionally found on Triple Offset Valves. By utilising a one-piece disc, Severn can add anti-cavitation trims, when conditions dictate, to help control the flow. This can also be paired with baffle plates when needed, enabling a Butterfly Valve to be utilised when severe service conditions may mean a standard Butterfly Valve would not be suitable or would have a significantly reduced service life.
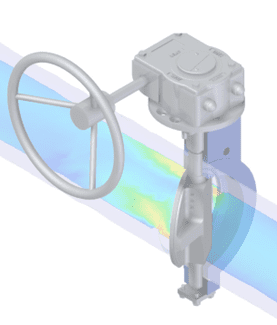
The OCT Triple Offset Butterfly Valve can be utilised for both control and isolation valve applications, enabling the end user to significantly reduce stock inventory and overall operating costs. Parts are standardised and interchangeable, meaning end users can have a reduced spares inventory leading to further cost reductions.
It also provides the end users with the option to potentially utilise one valve that can perform both the control and isolation functions within a system, rather than two – leading to significant reductions in operating and service costs and weight saving – this can be paramount for weight critical operations such as offshore installations.
Explore the design that has been inspired by engineering heritage and excellence to create a product that master’s isolation and control applications.
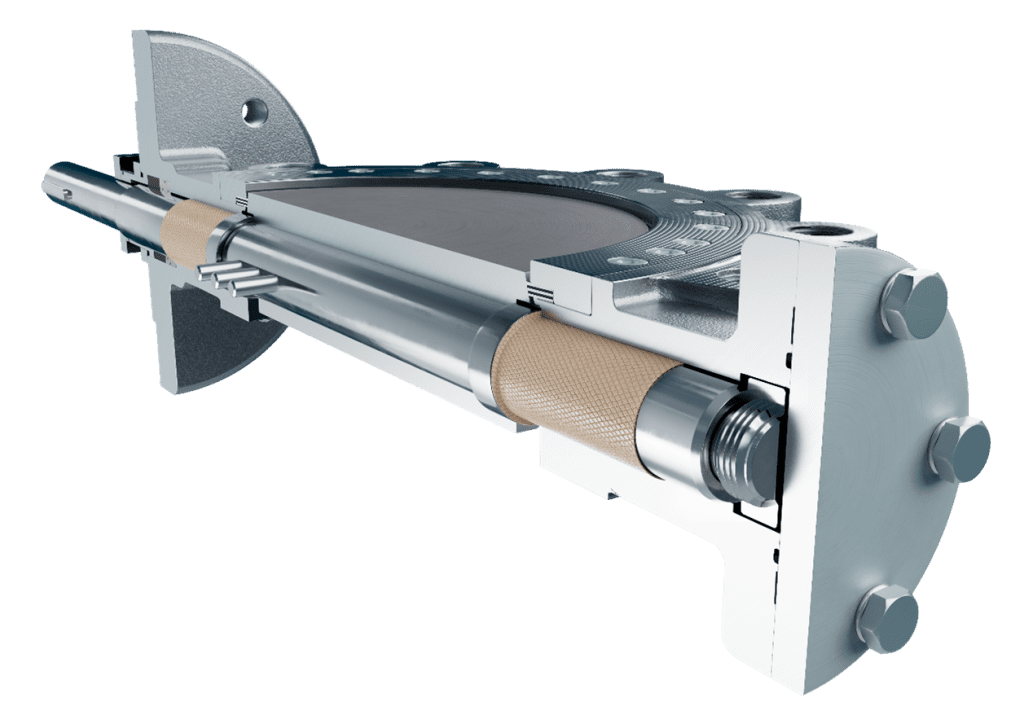
From the outset, Severn wanted the Oblique Cone Technology (OCT) to be unique in the Triple Offset valve market. Severn wanted to develop a product that not only solves an extensive range of issues for the customer with our “standard” product range, but to break tradition, and to design and manufacture a technically superior Butterfly Valve.
By utilising their comprehensive history with specialist butterfly valve design and manufacture, Severn have been able to develop a Triple Offset Butterfly Valve that performs both control and isolation duty in a single package. A valve designed from the outset to be re-used, upgraded, and provide an increased level of safety to the end user.
Severn have utilised its years of experience in manufacturing both the concentric and double offset Butterfly Valves to create innovative technology that pushes the boundaries of Triple Offset Butterfly Valve design. By looking at the traditional elliptical sealing concepts of Triple offset valves and combining this with circular sealing principals, Severn created its patented Oblique Cone Technology (OCT). In its most simplistic form, the geometry can be compared to a circular cone, by moving the point of the cone along one axis, this creates two different angles to the cone sides (forming an oblique cone), by taking a slice of this cone, it forms the sealing geometry of the OCT valve.
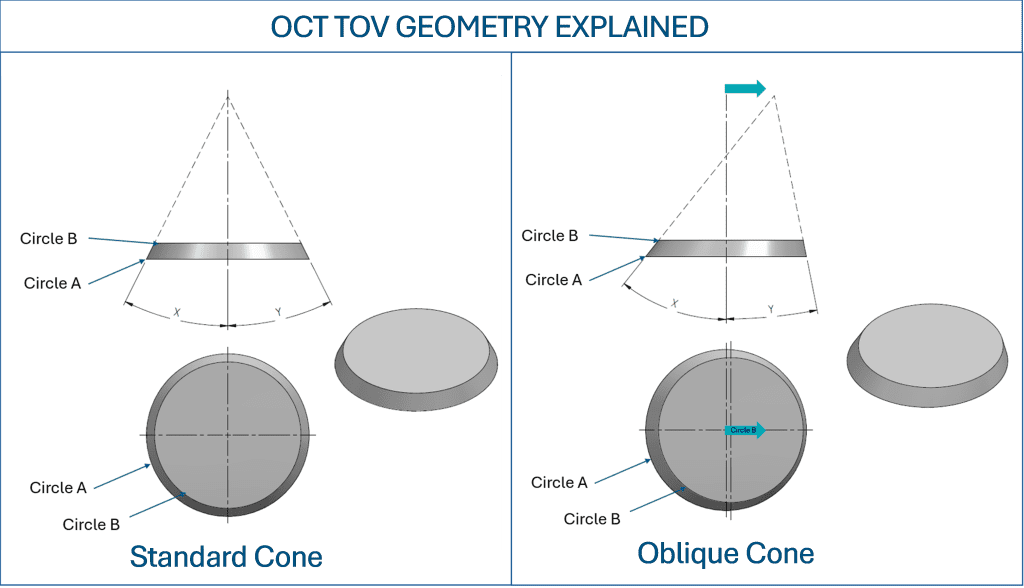
The benefit of this method means we maintain the principals of circular seals, thus providing an even seat load all-round the disc, therefore providing increased flexibility within the design to allow Severn to add different sealing options to the valve as well as specialist control trims such as anti-cavitation / low noise trims.
By understanding the foundational principals of Butterfly Valve design, Severn have a detailed knowledge of the interaction between each and every Butterfly Valve component. This combined with Severn’s Repair Intelligence philosophy and over 60 years of engineering excellence, customer solutions and end user feedback, problems can be anticipated and resolved before they occur and therefore increasing the lifecycle of the product and reducing costly unplanned downtime.
Severn additionally want to break the cycle of Butterfly Valves being a “throw away’’ commodity items. The OCT TOV Butterfly Valve is designed to be re-used, repaired, or upgraded on site with only basic tools. The robustness of the design means that the main components can be cleaned, soft goods replaced, and the valve can be reinstalled to provide extended years of reliable service. This not only reduces long term cost of ownership for the end user, but also reduces the environmental impact of the plant operations. Severn also install Fugitive Emission certified packing as standard in the OCT to further reduce the plant emission.
Flexibility and reliability come as standard in the OCT TOV Butterfly Valve. By using the principals of a Control Valve, Severn have streamlined and reduced the disc thickness to impede the flow as little as possible and maximise valve Cv. Fasteners have been removed from the disc, to eliminate the risk of them coming loose due to vibration and falling into the pipeline. The seal has also been mounted in the body rather than on the disc. This not only protects the seal by removing it from the direct flow path, but means the disc is thinner as well as giving Severn the option to add anti cavitation / low noise trims onto the disc when process conditions dictate.
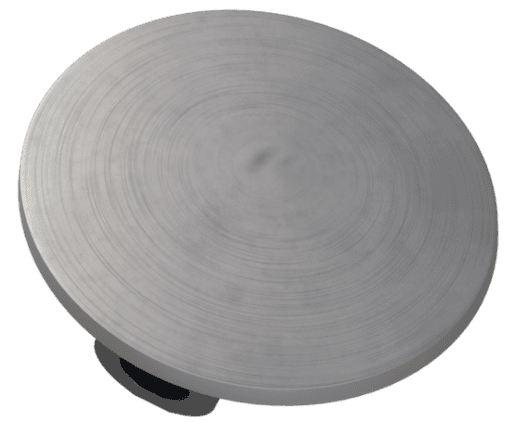
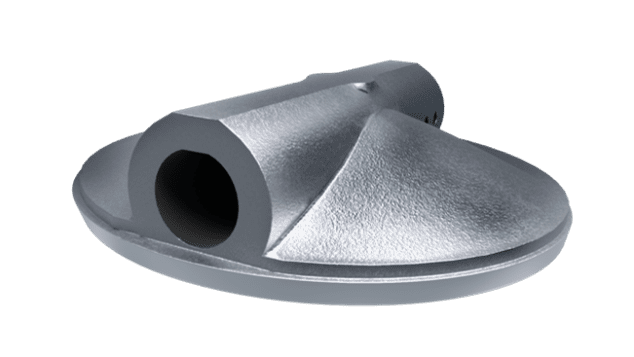
The OCT principle has been installed and operating in the field for over 10 years without issues, this coupled with countless amounts of testing and validation including fire testing, pressure testing, temperature testing and cycle testing, provide the end user with confidence in the robustness and reliability of the OCT Triple Offset Butterfly valve range and ultimately minimise down time and plant costs.
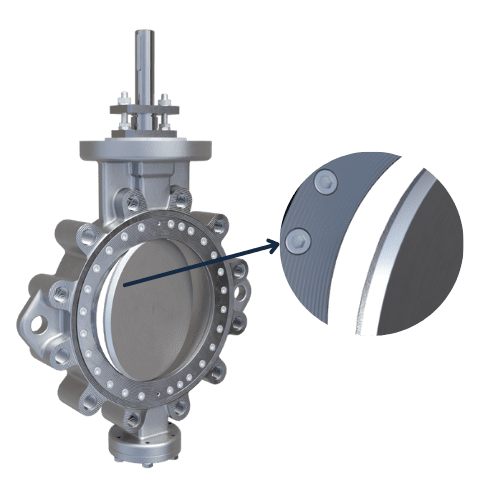