Severn manufacturer and deliver future proof pressure control valve to meet hydrogen growth demands
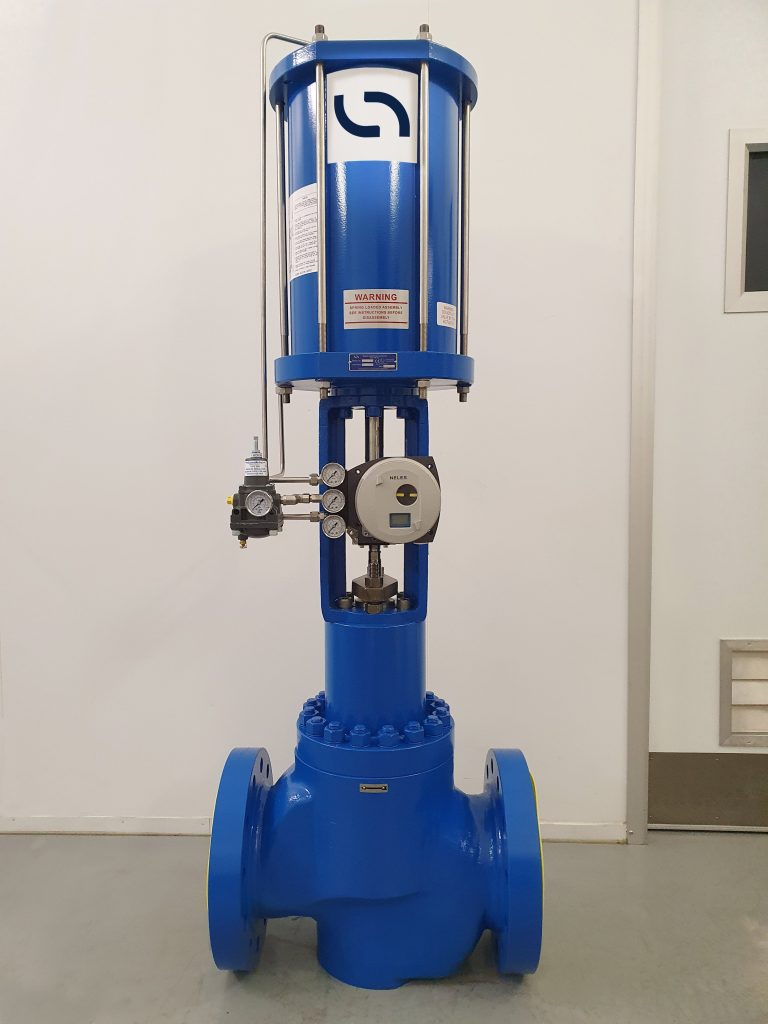
Industry:
Industrial Gas
Location:
UK
Project:
Hydrogen Gas Flow/Pressure Control Valve
The Challenge:
An Industrial Gas Client needed a solution for a control valve with low initial phase flowrate and the capability to operate at a high phase flow rate to meet future Hydrogen Gas Flow demand. Upon reviewing the process conditions and performing sizing calculations, it was predicted that a Phase 1 flow required a 2” valve trim & the future maximum demand required an 8” valve trim with a flow coefficient of 500 Cv.
However, in the short to medium term the required flow coefficient was only 40 Cv which would normally be provided by using a 2” valve, which could control down to a Cv of 1.58.
The client expressed a wish that the future demand should be met purely by a trim change only.
Finding a solution:
The Severn team made initial engagement with the client to fully understand the performance requirements that the customer needed and applied their extensive knowledge on the application. A swift coordinated approach by Severn’s IGP application and engineering team was needed and the teams worked closely to ensure the design was made to be future proof.
The product:
After identifying the clients requirements, the engineering team designed and manufactured an 8” Class 600 Fig 5413 CS Body, SS/FC Trim, 1CC 40 Cv, P2CN Pneumatic actuator with a Electro Pneumatic Positioner. A future trim set of 1CC 500 CV was also designed to be interchanged into the existing valve body without the need of any changes to the actuator configuration.
To avoid the complication to the end user, changing valves and valve sizes along with associated piping later in the plant’s lifecycle, Severn took on the challenge of providing a much smaller trim in the 8” valve, whilst retaining the ability to retro-fit the much larger trim for the longer term application.
The stroke of the much larger trim was retained which enabled the positioning system to remain un-altered when the larger trim was fitted. The seat platform also had to be carefully considered as the power actuator for the 8” valve trim could possibly deflect the seat gaskets causing detrimental damage.
The outcome:
The spares team have been able to quote for the client for the future trim set and when the demand is at fully capacity the after sales site service team will be ready to support the installation of the new increased capacity trim.
It was important for the client to find a vendor that has the technical knowledge and expertise, with a flexible approach to overcoming such a challenge, which made Severn the perfect choice.
If you want to read more of our case studies, you can find them by clicking the Case Studies button below or if you would like to contact us with an application, engineering or other valve query than click the contact us button.
Alternatively, you can download the full stage case study via the download button below.