DIT envoy to Ghanaian facility
Genesis SG, a partnership between Genesis Oil & Gas Services and Severn Valve Solutions (a Severn Glocon Group company), recently hosted Peter Courtney from the UK Department of International Trade at the Genesis SG service base in Takoradi, Ghana.
The purpose of the visit was to learn more about Genesis SG’s workscopes and future plans. As the UK’s Head of Trade in Ghana, Courtney is actively involved in the support and development of UK businesses operating in the country. He was joined by Selorm Kofi Dake, a Trade Advisor at the British High Commission in Ghana.
Genesis SG is a valve engineering company serving energy and industrial markets in Ghana. The visitors were given a tour of the workshops and met key members of the team. They discussed current and potential markets and looked at plans for a new workshop facility.
Douglas Fulton (Business Development Director) and Zahid Sadmaliyev (Senior Valve Technician) from Genesis SG coordinated the visit and explained the nature of the advanced technical services Genesis SG provides. The business is strategically aligned with the critical needs of Ghana’s energy markets. It provides specialist valve management and repair services locally, leveraging the international experience and technical expertise of Severn, combined with the local infrastructure and operations of Genesis.
“It was great to see partnership in action when we visited the facility in Takoradi,” says Courtney. “This is a good model for UK companies seeking to do business in Ghana. We look forward to visiting the facility again once the expansion project has been completed.”
Fulton adds: “Since Genesis SG was established in January 2018 it’s made impressive progress. Our valve services enable local operators to unlock better performance and reliability. It was a pleasure to show Peter and Selorm around the facility and they shared valuable advice about trade in Ghana.”
For more information on Severn Valve Solutions, please visit www.severnvalvesolutions.com
For more information on Genesis Oil & Gas Services, please visit http://www.genesis.com.gh.
For more information on Severn Glocon Group, please visit www.severnglocon.com.
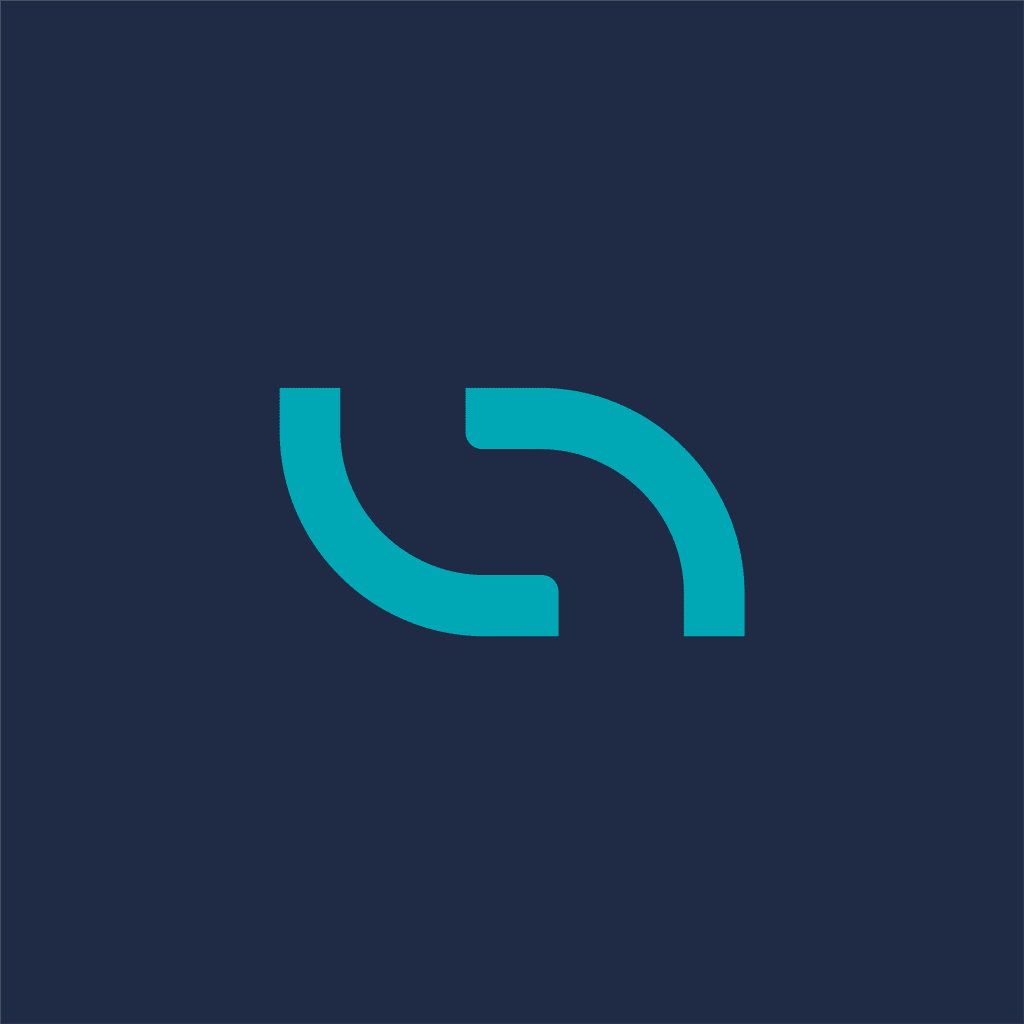
Ground-breaking wave energy converter prototype reaches the FaBTest nursey site in Falmouth for sea testing.
SG Technologies designed and manufactured the ground-breaking wave energy electrohydraulic control system at the heart of this quarter-scale device which has been created by Marine Power Systems. Following successful completion of pre-deployment tests in Milford Haven, it was towed to Falmouth for full deployment.
WaveSub harnesses energy from the continuous orbital motion of waves under the surface of the sea. It comprises an array of floats and tether lines which are connected to hydraulic generators. As the floats move with the waves, hydraulic energy is created. This is smoothed via the hydraulic circuit and turns an electrical generator with grid-compatible electrical output.
Growth in the renewable sector continues to gather pace, and Severn is committed to developing new technologies that help capture energy from natural sources.
Severn manufactures and supports high quality valves for the energy industries. Its control, choke and small bore subsea valves are pre-eminent in the global market, underpinning the reliability and high performance of business-critical client infrastructure.
Severn’s global reach, technical prowess, and collaborative approach – all founded upon a heritage of British engineering excellence – help to assure production continuity for clients and reduce the prospect of costly downtime.
Its understanding of the life-cycle of assets positions Severn to offer end-to-end engineering solutions, enabling clients to meet their core imperatives: safe operations and minimum downtime.

Severn extends its reach.
Severn’s model for establishing world-class valve engineering skills locally in key production markets that have previously lacked investment continues to reap rewards. This led to the recent launch of GenesisSG in Ghana, a relative newcomer to the oil and gas market that is seeking to ramp up production and push for energy independence.
The overarching goal is for Severn to extend its reach and to address capability gaps, enhancing the long-term prospects of regions that have faced socio-political issues or experienced rapid growth of new processing industries. It involves blending Severn’s advanced valve engineering expertise with infrastructure support and knowledge of local partner organisations. This is applied strategically to facilitate better valve population management alongside training and development of local engineers.
Successful ventures in Iraq and Kazakhstan have led to significant performance improvements for organisations including Basra Gas Company. A small team of valve experts from overseas mentors local engineers, progressively handing over greater levels of responsibility. The ultimate intention is to redeploy the expats to new markets requiring support, once local engineers are fully empowered to handle the technical demands of proactive valve management.
The approach is now being used as a blueprint for the rollout of similar ventures in other markets that require specialist valve engineering support so Severn extends its reach.
Repair Intelligence boosts FPSO performance.
Severn’s longstanding experience optimising valves for the harsh challenges of the North Sea environment continues to underpin offshore success at a global level. This was evidenced in a recent job for the Jubilee FPSO operated by MODEC off the Ghanaian coast.
“A combination of extreme environmental conditions and high performance demands were pushing flow control valves on the FPSO far beyond their original specification,” explains Adam Eckersley, Technical Engineering Manager at Severn Unival. “Valve components were exposed to warm aerated seawater, and the resulting corrosion led to performance issues and regular production interruptions, with significant financial consequences. The damage was so severe, that in some cases valves had to be replaced or overhauled on a six-monthly basis.”
In 2013, Severn upgraded the valves with an Inconel cladding. This proved to be an effective solution, resulting in reliable and efficient operation. However, at a later date the FPSO began to experience production challenges associated with assets outside the valve population. At this point, insights gathered by Severn during inspections of internal valve components during the overhaul unlocked new measures to enhance the vessel’s technical capabilities, to improve safety, reliability and performance.
Aberdeen-based oil and gas consultancy Core was appointed by MODEC to develop a strategy to overcome the FPSO’s wider performance issues. Overlaying Core’s analysis of actual process conditions and requirements with Severn’s Repair Intelligence from the earlier overhaul facilitated more precise application of engineering skills to enhance the vessel’s performance. A critical enabling factor was Core’s revelation that the vessel’s actual process temperature was 40°C as opposed to the specified 60°C. This had a major impact on material selection, clearing the way for Super Duplex to be used.
“All the pressure control valves and flow control valves have been switched for highly-engineered Super Duplex replacements manufactured by Severn,” Adam continues. “They were completed and shipped four weeks ahead of the planned shutdown earmarked for their installation. And the Inconel-clad FVs supplied in 2013 have been overhauled, upgraded and retained as spares.”
LNG safety system underway.
Engineers from Severn Glocon Technologies have visited Korea to commission a High Integrity Pressure Protection System (HIPPS) supplied to shipbuilder DSME for a Floating Storage and Regasification Unit (FSRU).
The LNG FSRU vessel, BW Magna, has a capacity of 173,400 cubic metres. The HIPPS has been integrated and installed by Severn Glocon Technologies to protect the pipeline during the unloading of gas, enhancing safety for the FSRU and the downstream equipment and pipeline in the docking terminals it connects with.
HIPPS are not mandatory on FSRUs, but it’s increasingly recognised that they provide a superior level of safety and reliability. Situated between high-pressure upstream and low-pressure downstream units, they contain media if over-pressurisation is likely to occur, rather than venting.
The system supplied to DSME operates at a working pressure of 117 barg. It comprises two 18” 900-class manual valves, a Sella Controls logic solver and three pressure transmitters.
Severn Glocon Technologies is a leading provider of HIPPS, and parent company Severn Glocon has extensive LNG experience having manufactured severe service valves for megaprojects including Ichthys and Gorgon. Site Manager Tim Blake says HIPPS integration and installation requires a wide range of engineering and functional safety expertise.
“Effective HIPPS integration demands electronic and mechanical engineering skills, with software engineering input sometimes needed as well,” he explains. “It’s important that these specialist engineers interrogate the design brief and collaborate with functional safety professionals. This is where using an independent integrator offers a major advantage. At Severn, we employ all of these professionals inhouse.”
Additional safety measures on the FSRU include alarms, a shutdown system, blow down system and safety valves, as per industry-specified standards. The benefit of adding HIPPS is that it is a simple, proven solution which can operate independently of the wider vessel system.
Plant support is booming for Severn.
The cautious global outlook that characterised the oil and gas industry for the past four years has driven a renaissance for established plant. Severn’s heritage in advanced engineering services for existing valve populations puts it at the forefront of growth in this arena. Since 2014, our established plant division Severn Unival has enjoyed exponential growth of 400%, putting its annual order book at £75m, emphasising that plant support is booming for Severn.
Divisional managing director Colin Findlay says leading operators are changing their approach to valve management. The depressed oil price drove a focus on operational efficiency, leading to a wave of new investment to improve the performance of existing assets. Recognising the level of dedicated engineering skill and expertise required to optimise control and choke valve performance, many operators have held competitive technical tenders to outsource this element of plant management efficiently. As the market picks up, this activity is accelerating with operators seeking to maximise performance and productivity.
“Technology is the core driver of efficient and reliable plant operations,” Colin explains. “Following the volatility of 2014 and the prolonged downturn experienced since, oil and gas operators have been keen to find stability and certainty. Investing in existing plant is the most prudent way to achieve this, and operators that continue with this approach alongside investment in new projects will have much surer foundations as the market begins to pick up again.”