As the world turns its attention to hydrogen as a primary energy resource, equipment manufacturers are gearing up to manage it. Richard Laukam, ValvTechnologies, and Tim Webb, Severn, discuss the pivotal role of valves in supporting a hydrogen economy.
At Present, hydrogen is dominating the headlines worldwide. This is no surprise, as this versatile fuel seems destined to play a crucial role in the world’s transition to a low-carbon economy. As the simplest and most abundant element in the universe, hydrogen offers great promise. The International Energy Agency (IEA)’s ‘Future of Hydrogen’ report asserts that, globally, clean hydrogen is benefitting from unprecedented political and business momentum, with both policy initiatives and projects expanding rapidly.1
The report suggests that there is currently a major window of opportunity to upscale hydrogen technologies and reduce associated costs, thereby enabling the broad use of hydrogen worldwide. In keeping with this, countries across the globe are announcing national strategies that rely on hydrogen to address environmental concerns without weakening energy security.
Scientists have studied hydrogen as a source of energy since the 1800s, and it has been an essential industrial feedstock and fuel for decades. Today, however, it is attracting considerable interest due to its potential to decarbonise major economic sectors, such as power generation, long-haul transportation, construction, manufacturing, chemicals, iron and steel.
Existing and future hydrogen infrastructure
Existing technologies enable hydrogen to produce, store, move and use energy in a variety of ways. It can be produced from renewables, nuclear, natural gas, coal and oil. In gaseous form, it can be transported by pipelines, and in liquid form, it can be transported by ships (much like LNG). In addition, it can be transformed into electricity and even blended with methane to power homes and industry, as well as into fuels for cars, trucks, ships and planes.2
Hydrogen has been used in refineries for more than 40 years. The gas is produced by steam methane reforming (SMR) in a process that emits carbon pollution. This product is commonly referred to as grey hydrogen. However, green hydrogen has been proven, at scale, using renewables to power methane pyrolysis or water electrolysis. Although there remains some technological uncertainty in many new applications – and the hydrogen infrastructure will require new networks and storage, as well as integration into gas and electricity networks – its potential is clear. Many countries are taking first steps towards the investment and deployment of hydrogen.
Safety concerns
As engineers worldwide focus increasingly on hydrogen, they are well aware it diffuses readily through materials, including the base metal substrates and coatings of the isolation valves that are critical to safe hydrogen processing. Christian Tae, Policy Analyst, Climate & Clean Energy Program, Natural Resources Defence Council, wrote a piece on the safety concerns behind the use of hydrogen, and underlined that whilst there are hazards to consider, this is not something that the industry has not dealt with before.3
Indeed, gaseous hydrogen, when mixed with omnipresent oxygen in the air, can self-ignite (whereas liquid hydrogen is far less volatile.) Therefore, hydrogen infrastructure of the future will require the use of both isolation and control valves to keep hydrogen flowing safely. Zero-leakage isolation valves will be needed to prevent leaks both externally and internally – from the valve stem or body/bonnet joints, as well as through the ball and seat. Control valves must operate with precision, preventing external leakage.
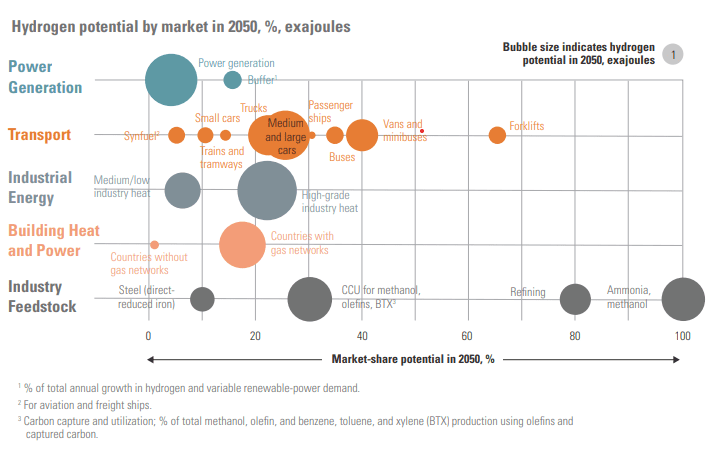
API 641 and fugitive emissions
The API 641 standard for fugitive emissions from quarter-turn valves was released in late 2016. As with the earlier standard, API 624 for rising-stem valves, this new standard is the type test for quarter-turn valves, gauging their low-emission performance during an accelerated life cycle.
API 641 applies to all stem-seal materials. To pass, the valve cannot allow leakage of more than 100 ppmv for the duration of the test. The API test standard calls for 610 cycles of the valve, under extreme temperature fluctuations, thereby evaluating emission performance during an accelerated life cycle.
Through and external leakage standards
The most stringent ANSI standard – Class VI, for hydrogen service – addresses through leakage between the valve’s ball and seat. ISO 15848-1 addresses external leakage from a body or stem joint leaking to the atmosphere. The standard, at the highest level (AH), is typically achieved with bellows seals or an equivalent stem (shaft) sealing system for quarter-turn valves. ValvTechnologies achieved class AH using fugitive emissions packing as opposed to bellows seals.
Helium to hydrocarbons to hydrogen isolation
ValvTechnologies initially developed its V Series with RiTech® H zero-leakage valves for helium service, processing high-purity silicon for a US manufacturer of semiconductors. The manufacturer successfully used nearly 5000 of the zero-leakage valves from 2004 to 2015, when it closed due to global trade restrictions. The valve continues to be used for select hydrocarbon processes – with either pure or partial hydrogen – in multiple refineries worldwide. It is also suited for the emerging hydrogen market.
Achieving zero leakage in hydrogen service
To ensure zero hydrogen leakage, these valves (both balls and seats) are coated with a proprietary chemical solution and compressive
spray technique that fills and seals the inherent microcracks and porosity of base metals. This proprietary process is called RiTech, for robotically-integrated technology. The valve components, whether manufactured from chromium carbide or tungsten carbide, are saturated with the chemical solution at room temperature, and then fired to chemically bond the coating and substrate.
This occurs in a robotically-integrated, high-velocity oxygen fuel spray booth, reducing porosity to zero and preventing even minor infiltration by hydrogen molecules or corrosives. This coating is optimum for impure hydrogen, and for pure hydrogen at pressures less than 3500 psi. If pressures exceed 3500 psi, the company recommends a spray-and-fuse process. In addition to material coatings to maintain zero leakage, an integral seat eliminates the possibility of gas escaping between a separate seat and seat pocket. A Belleville spring forces the upstream seat into the ball and, in turn, into the integral seat. The spring load is very high, ensuring that hydrogen cannot leak past the seat. With such tight isolation, the valves produce higher operating torques which are critical for the positive shut-off demanded in hydrogen service.
Control valve considerations
Isolation and control valves have different roles to play: the control valve regulates fluid flow by varying the flow area, as signalled by a controller, to manipulate pressure, temperature and liquid level. To eliminate external leakage, globe control valves with rising stems use live-loaded, high-integrity gland packing, or even a bellows seal, but continue to provide precise control. These valves typically meet both international and ASME standards. When selecting a control valve, it is important to look for multiple trim options to ensure that the valve meets both current and future requirements. As demand for hydrogen ramps up, the selected valves can be retrofitted for precise control.
Looking to the future
It is clear that isolation and control valves will play an important role in the future global hydrogen market, in order to safely contain and control hydrogen in both liquid and gaseous form. ValvTechnologies and Severn will continue to develop and refine products to meet the exacting performance and safety standards of the energy transition.
References
1 – ‘The future of hydrogen’, International Energy Agency (IEA) (June 2019).
2 – ‘H2@Scale’, US Department of Energy, Office of Energy Efficiency and Renewable Energy, www.energy.gov/eere/fuelcells/h2scale
3 – TAE, C., ‘Hydrogen Safety: Let’s Clear the Air’, NRDC, (14 January 2021), www.nrdc.org/experts/christian-tae/hydrogen-safety-lets-clear-air
- 4 – ’Hydrogen Strategy: Enabling a Low-Carbon Economy’, US Department of Energy, (July 2020), p. 10, www.energy.gov/sites/prod/files/2020/07/f76/USDOE_FE_Hydrogen_Strategy_July2020.pdf
More News
All News- Posted: 30 June 2025 How to Boost the Durability and Functionality of LNG Compressor Anti-Surge Valves
- Posted: 23 June 2025 How Highly Engineered Compressor Surge Control Improves LNG Plant Performance
- Posted: 16 June 2025 Surge Control for Liquefied Natural Gas (LNG) Compressors: Three Reasons to Make it a Priority
- Posted: 20 January 2025 Meet the Severn IEW 25 Team
- Posted: 25 November 2024 Severn Secure Success with Sour Service Application and Fugitive Emissions Leakage Rate A
- Posted: 29 October 2024 Severn Aberdeen: Your Go-To Partner for OEM and Third-party Valve Solutions.