Discover how engineering excellence and heritage has driven Severn’s OCT TOV Butterfly Valve to deliver unmatched reliability in Seawater environments.
Severn’s research & development team has designed a Butterfly Valve that solves the problem of galvanic corrosion and meets strict fire test standards. Utilising the over 60 years of engineering excellence, the team of technical experts achieved this by using Severn’s patented Oblique Cone Technology (OCT). The OCT-SW takes this patented technology to the next level by eliminating the need for graphite in the seal and maintaining firesafe capability.
What is galvanic corrosion and its costly effects?
The impact of galvanic corrosion on critical assets due to seawater process conditions is an enduring problem for offshore oilfields. At best, it increases the workload and repairs associated with planned shutdowns. At worst it can result in rapid or unexpected damage, leading to unplanned or emergency shutdowns. Either way, it is a costly problem which harms efficiency, putting additional pressure on plant operating costs. However, Severn have utilised their engineering heritage, research and development & repair intelligence knowledge to develop a valve that deals with the issue of galvanic corrosion head on.
Why does galvanic corrosion occur? The cause of galvanic corrosion (also referred to as ‘dissimilar metal’ or ‘bimetallic’ corrosion) is an electrochemical reaction between two different conductive materials in close proximity. It results in one – the least noble of the two – being preferentially corroded. To combat this risk, the general rule is ‘do not mix metals’. However, when it comes to the design and development of assets for harsh offshore environments, things are rarely that straightforward.
Modern critical safety systems used on offshore sites are often highly sophisticated
to cope with the extreme natural conditions and industrial challenges with which they must contend. They come with extreme technical demands but must manage physical ones too; systems that need to feed water to combat fires must be durable enough to cope with the corrosive effects of the sea. Seawater service valves play an integral role in the process and their ability to either supply or isolate sections of the water line is a vital safety feature. Therefore, eliminating galvanic corrosion while maintaining firesafe credentials has been an enduring challenge for the industry.
In recent years, the use of graphite sealing technology has surged. Graphite’s extreme range of properties and characteristics makes it an ideal material in many ways. It is soft, flexible, and easy to cut, but it has high heat resistance and is almost inert. However, it is also the only non-metal that can conduct electricity. Furthermore, its nobility exceeds that of noble metals including stainless steel, bronze, and titanium. Yet it is often paired with these materials in valve manufacture, in the form of seals, packings and gaskets. From a galvanic corrosion perspective, graphite has become not only the solution to problems but can often be the cause.
Traditionally, Triple Offset Butterfly Valves have used graphite materials in their construction, which can cause galvanic corrosion in seawater applications. This is a problem because it can significantly reduce the effectiveness of the valve’s sealing components, compromising safety and leading to potential costly unplanned downtime.
By working closely with end users and operators, Severn has recognized this issue, and with its significant engineering heritage and technical expertise, has designed a long-term solution. The Severn team of engineering experts designed a valve that either replaces the graphite components completely or stops them from contacting the line media. This significantly reduces the risk of galvanic corrosion in day-to-day operations and ensures the highest level of safety. Ensuring you achieve safe operations and minimal downtime.
The Oblique Cone Technology (OCT) Seawater (SW) Triple Offset (TOV) Butterfly valve is a revolutionary type of valve designed primarily for use in saline applications, such as offshore oil and gas operations. These valves play a pivotal part in safety systems, as they play a crucial role in firewater systems. Due to Severn’s engineering heritage and technical expertise in the oil and gas operations sector, this valve has been designed with over 60 years of engineering excellence ensuring it helps the end user achieve their core remit of safe operations and minimum downtime.
Severn has developed a hybrid polymer metallic seal that moves away from the use of graphite laminates. By utilising a primary metallic seal with a secondary polymer seal, not only have Seven removed the graphite from the seal but have additionally increased the valves isolation sealing capabilities and maintained the firesafe performance crucial for such critical applications. This coupled with isolating any graphite gaskets and packings from encountering the line media means that at no point during the normal operation of the valve do the graphite and seawater mix, eliminating the risk of galvanic corrosion and the costly effects it can have on production.
In addition to addressing the corrosion problem, Severn’s Butterfly Valves also meet important fire test standards such as API 6FA, API 607, and ISO 10497 accreditations. As such the OCT Valve is certified fire-safe and can be relied upon in critical emergencies for the end user and operators, ensuring safe operations and minimal downtime.
The team also took steps to ensure the valve design could not generate a spark and risk starting a fire itself. They followed the ISO/IEC 80079-36:2018 ATEX standard and ensured that no static charge could build within the valve. This additional element of care renders the new OCT-SW valve design suitable for a wide range of applications, beyond seawater service further emphasising the versatility of the valve design.
The OCT-SW can be manufactured from corrosion-resistant materials such as Aluminium Bronze, Super Duplex, and Titanium, with the added knowledge that anti-blowout protection comes as standard. Available in standard and non-standard face to face dimensions and various body styles such as lugged and double flanged, the valve can be easily retrofitted into existing pipeline spaces and is an ideal upgrade when operators are experiencing issues with galvanic corrosion.
Severn understands the ongoing challenges operators face with reducing and eliminating fugitive emissions and have created a technical solution with the design of its Oblique Cone Technology Triple Offset Butterfly Valve.
Operators are under increasing pressure to reduce fugitive emissions for both onshore and offshore assets in order to achieve their core imperatives of safe operations and minimum downtime. Severn realises the role they play in today’s climate conscious world to help reduce and eliminate fugitive emissions from valves. Utilising the engineering heritage and extensive knowledge in severe service applications, Severn ensures it can offer the most suitable product for the end user.
Through Severn’s ‘Repair Intelligence’ and close operating relationships with end user operators, Severn has been able to understand the difficulties facing operations in the specification, purchasing and servicing of Control, Choke and Butterfly valves that are critical to reducing fugitive emissions across industrial facilities. Severn prides itself in offering technical solutions that perform no matter how severe or critical the application is. Ensuring that the end user gains the best valve performance and reduced maintenance costs over the lifecycle of the valve.
It has long been understood that approximately 60% of fugitive emissions come from valves. Even more so 80% of those emissions are related to the stem/shaft seal. Naturally, the focus is on this area with the relative fugitive emissions standards such as API 622 and ISO 15848. What is often misunderstood is the requirement for the standards to be applicable across varying temperature and pressure differentials. For this reason, Severn has 43 different certificates for sealing systems in valves based on their application requirements, up to 10,000 Psi and 425ºC. By utilising a range of materials from filled graphite through to custom PTEE-based compounds, Severn has, coupled with novel packing designs, been able to achieve tighter leakage rates that had previously been achieved with standard packing sets.
It is vital for the end user to understand the leakage class requirements when fugitive emissions are concerned to prevent over or underspecifying the solution. We often see “fugitive emissions” specified without clarification of the requirements. The various requirements from TUV through API and ISO specifications require different testing methodologies and even different testing mediums. This means that the testing standards are not directly comparable to each other. Severn often see the specification of “Low-e” or “Low emission” packing without reference to the specification. In some instances, these packing sets can have allowable leakage of up to 500ppm, many times that of systems tested to the ISO 15848-1 standard and potentially resulting in detrimental reduced on-site performance and / or higher maintenance costs.
Severn has focused and will continue to focus its testing efforts on ISO 15848 standards as it is understood that these offer the widest range of qualification options whilst not utilising harmful greenhouse gases that can be emitted using some API methodology. The fact that sealing systems are tested on the valves they are designed for and not a standard test fixture ensures maximum customer confidence in our products performance and reliability.
Severn have focused on passing some of the most stringent testing with class A leakage classes and up to 40,000 operations available for some applications. Ensuring that performance is at the heart of our product range, and you achieve your core remit of safe operations and minimum downtime.
To further the commitment to reducing fugitive emissions and reduce the burden on end users to meet tightening specifications, Severns OCT Triple Offset Butterfly Valve offers the fugitive emissions packing sets as standard fitment on all standard valves in the range. Ensuring that the end user experiences maximum valve performance in all applications.
Severn’s engineering heritage and technical expertise have led to the OCT TOV Butterfly Valve being future-proof for changes in the process conditions to provide increased versatility for the end user.
From the outset, Severn made flexibility a key driving force in the design of the Oblique Cone Technology (OCT) Triple Offset (TOV) Butterfly Valve. Due to Severns extensive diverse engineering heritage and excellence, our expert team of engineers understand that processes and application product demands change over time, whether it is the process conditions or the overall requirements of the valve for the end user. Due to this understanding, the Oblique Cone Technology Triple Offset Butterfly Valve has been designed to incorporate multiple seal options, all fully interchangeable with each other, providing maximum application diversity and usability to ensure safe operations and minimum downtime.
The Laminate seal is the “traditional” Triple Offset Valve seal and consists of multiple metal and graphite layers providing isolation sealing.
The OCT HS seal is a hybrid polymer metallic seal, this seal benefits from a primary metal seal and secondary polymer seal, this provides a reliable and repeatable bubble tight seal time after time. This can also be paired with PTFE packings when graphite being in contact with the line media is a concern. The polymer seal is fully compliant with EN ISO 80079-36 (ATEX).
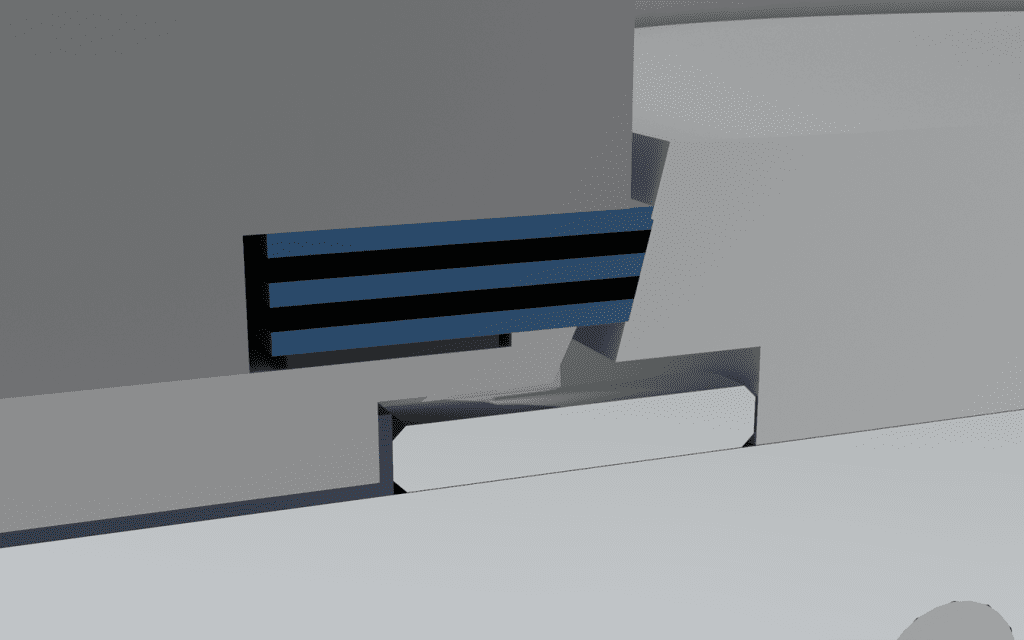
The OCT SW Valve takes the hybrid sealing to the next level with its versatile high performance. Severn utilises the OCT-HS seal and has designed a valve that ensure there is no graphite in contact with the line media to remove the risk of costly galvanic effects such as internal corrosion leading to valve failure. Whilst doing so the OCT-SW also maintains firesafe certification.
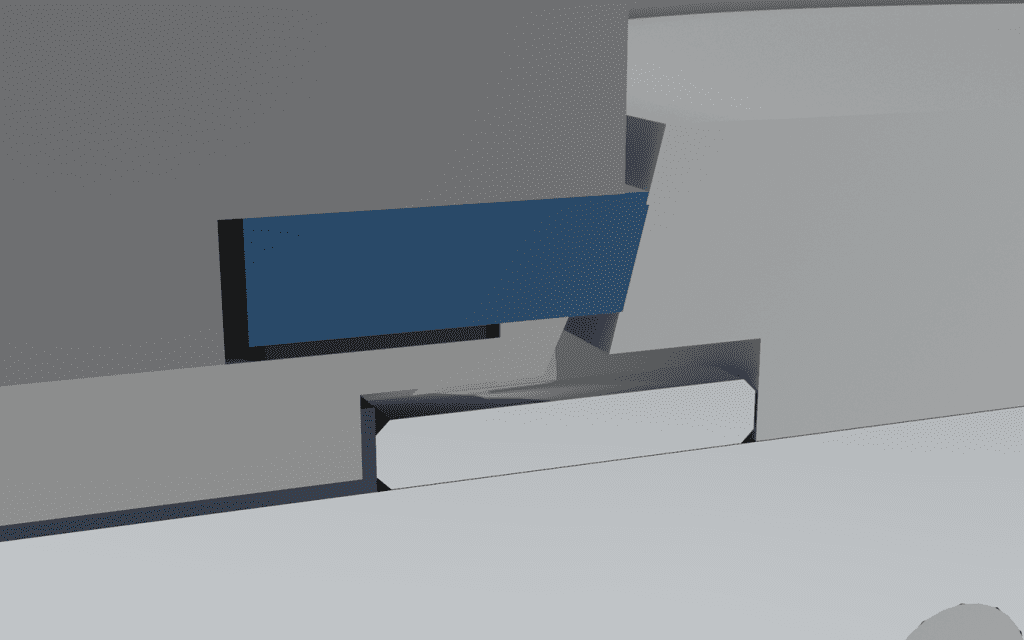
Should the sealing requirement not become as critical, and process conditions become more arduous, the Laminate and Hybrid seals can be changed for the OCT-SS solid seal. As the name suggests it is a solid metallic seal, that can be made from hard-wearing alloys to add longevity to the sealing life of the valve in arduous conditions and can offer a control valve seat leakage.

Based on Severns comprehensive history of severe service control, our team of engineering experts work closely with operators and end uses to identify the correct seal and material selection to provide the maximum reliability and productivity further ensuring minimum downtime.
All the OCT seals are interchangeable and can be upgraded without the need for main valve components being replaced, further emphasising the OCT TOV Butterfly Valves versatility. The fully in field serviceable valve can be upgraded on-site without the need for specialist tools or knowledge, this further ensures that costly unplanned downtime and site waste is kept to a minimum, along with potential loss in production for the end user. All the seal options can be changed on site within a small space of time to ensure site maintenance costs are reduced by upgrading the existing valve rather than discarding and replacing with a commodity product each time.
Each OCT valve is specially designed to be versatile and ensure it has multiple purposes for multiple conditions whilst still delivering maximum performance. With the introduction of the interchangeable seal, these can be easily swapped out to match the end users’ requirements, should they change.