Exploring the innovative features and engineering principles of Severn’s OCT TOV Butterfly Valve that puts safety first.
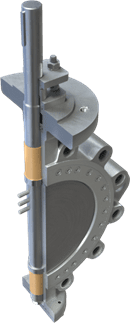
At Severn, safety is paramount in the design of our products. With our background in safety-critical industries, Severn understands the importance of safety first for both our customers and employees.
As well as adhering to the strictest industry standards, Severn have identified that shaft blowout prevention was paramount to our end users and the wider industrial and process industries for improved valve performance and reduced operational downtime.
Butterfly Valve shafts are designed to connect to the disc with either dowel pins, taper pins, or keyways. The separation of the shaft and disc in service can be catastrophically dangerous. If any of these parts fail, the shaft may be ejected from the valve body. Shaft blowouts can occur when a coupling mechanism fails, therefore, disconnecting the shaft from the disc. With the pressures in the system, it may eject the unrestrained drive shaft through either end of the valve.
Not only is this projectile a huge safety concern but has the potential to compromise the pressure envelope of the valve allowing process to escape into the atmosphere.
Severn has designed all their Triple Offset Butterfly Valves as standard with anti-blowout incorporated at both ends of the valve. This negates any chance of the shaft blowing out if the pins were to fail. The reduced shaft diameter at the drive end ensures the shaft cannot blow out through the packing follower.
On the blank end of the valve, Severn have multiple features which prevents shaft blowout. The anti-blowout ring on the threaded shaft end ensures positive engagement without the need for additional fasteners. The blank end plate is locked in place and is designed to withstand full rated test pressures.
Dual anti-blowout devices are standard on the OCT TOV Butterfly Valve, meaning that even if the gland is removed, the secondary internal anti-blowout device will stop ejection of the shaft under the pressure, thus increasing both operator and plant safety.
Severn have designed their Triple Offset Valves to exceed the minimum wall thicknesses stated in ASME B16.34. Instead of just using the minimum allowance, Severn have gone above and beyond to ensure the safety of our products in the field for our customers.
Within Severn’s Triple Offset Butterfly Valve is a corrosion allowance. This means that the valve can afford to concede material to corrosion over time without affecting the pressure containing integrity or safety of the valve. The amount of corrosion may vary depending on the environment the valve is working in, but due to Severn’s engineering heritage and excellence, the OCT TOV Butterfly Valve has been designed to withstand changes in working environments and process conditions.
High MAST figures and safety factors are key when designing the Triple Offset Butterfly Valve. MAST is the Maximum Allowable Shaft Torque a quarter turn valve shaft can withstand during operation without mechanical failure. With Severn using higher MAST figures on their Triple Offset shafts, this helps maintain the structural integrity of the valve.
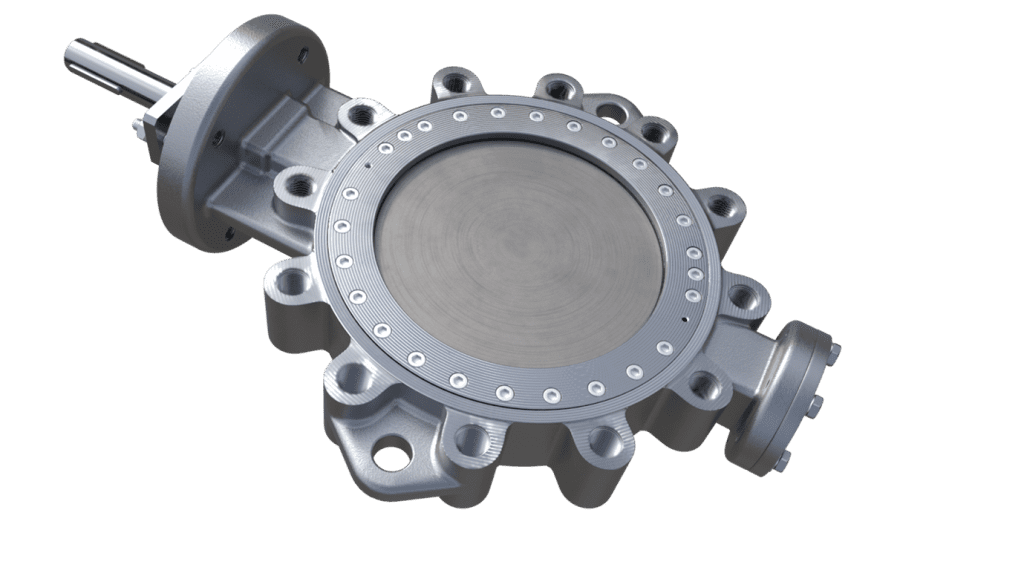
Sizing actuators correctly is a credit to Severn’s engineering excellence. Actuators, gearboxes, or any form of obturator that drives a quarter turn valve must be sized correctly by using the correct input and output torques. By torque testing the physical products prior to final inspection, we can compare the physical torques against our theoretical torques to maintain accuracy and consistency across the range.
Safety has always been at the forefront of Severn’s designs, and this is paramount in the 8500 Butterfly Valve range.
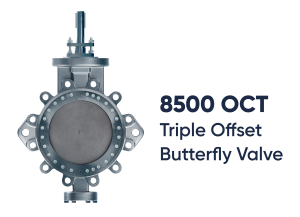
With over 60 years’ experience in the design and manufacture of Butterfly Valves, Severn launches a range built on decades of learnings and innovative engineering.
In the dynamic landscape of industrial engineering, innovation often stems from a rich heritage of expertise and an unyielding commitment to excellence. Severn Glocon, a renowned name in the world of valve design and manufacturing, have once again proven this statement true with the unveiling of the superior Oblique Cone Technology (OCT) Triple Offset (TOV) Butterfly Valve. This development represents Severn’s commitment to innovation in the realm of process and industrial energy markets, promising enhanced performance, reliability, and efficiency.
Engineering Heritage: The Foundation of Excellence
Severn’s journey to engineering eminence is woven with a tapestry of innovation and dedication stemming back over 60 years. With an engineering history extending back to 1957 and the design and manufacturing of Globe Control Valves, Severn has continuously pushed the boundaries of valve technology and design, earning a reputation for precision engineering and unmatched quality. Drawing from this extensive engineering heritage, Severn has consistently delivered solutions that exceed industry standards and address the evolving needs of diverse sectors.
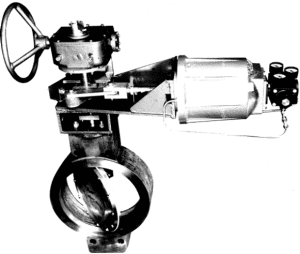
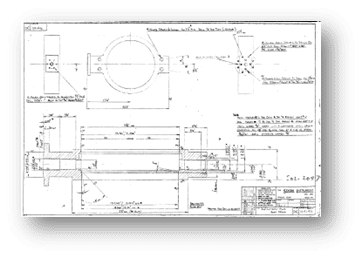
Unveiling the Oblique Cone Technology (OCT)
At the heart of Severn’s latest engineering triumph lies the OCT TOV Butterfly valve, a revolutionary advancement in Butterfly valve design and performance. Unlike traditional Butterfly valves, which often suffer from limitations in sealing performance and durability, the OCT TOV Butterfly Valve introduces circular sealing geometry.
Unlike traditional triple offset designs that use an ellipse. The benefit of circular geometry is that it provides a uniform sealing load around the circumference of the sealing diameter, providing a reliable and repeatable shut-off. By using circles rather than ellipses, it allows Severn to use proven circular sealing knowledge and incorporate this into the TOV.
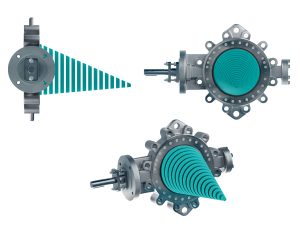
Incorporating Severn’s ‘Repair Intelligence’ knowledge which involves providing real market feedback from extensive in-depth analysis from failed valves. Severn have designed each facet of this valve to provide the most accurate, reliable, and robust service capability possible whether managing critical processes in Oil & Gas refineries, Chemical Plants, or Power Generation facilities, the OCT TOV Butterfly valve ensures the end user achieves their core remit of safe operations and minimum downtime.
Advantages for Process and Industrial Energy Markets
The introduction of the innovative OCT TOV Butterfly Valve designed by Severn signifies a paradigm shift in valve technology, offering a host of benefits to the Process & Industrial Energy markets
Enhanced Performance: Severn have designed each facet of this valve to provide the most accurate, reliable, and robust service capability possible to help the end user achieve their core remit of safe operations and minimum downtime.
Extended Lifecycle: Process conditions can change with time. Severn have ensured the interchangeability of the seal, should the sealing requirement not become as critical, or process conditions become more arduous.
Increased Safety: At Severn, safety is paramount to the design of our products and ensured that whilst adhering to the strictest industry standards, have incorporated shaft blowout prevention as a vital addition to the design of the valve to increase suitability for end users and the wider industry.
Versatility: Utilising Severn’s extended history of engineering excellence, the OCT TOV Butterfly valve has been designed for both superior control in both throttling and modulating services, whilst additionally providing a repeatable seal for isolation duties.
Environmental Sustainability: To further the commitment to reducing fugitive emissions and reduce the burden on end users to meet tightening specifications, all Severn’s OCT triple offset butterfly range offer the fugitive emissions packing sets as standard fitment on all standard valves in the range.
Severn’s relentless pursuit of engineering excellence has culminated in the development of the OCT Triple Offset Butterfly Valve – a testament to the company’s unwavering commitment to innovation and customer satisfaction. As industries worldwide seek ever-improving solutions to their operational challenges, Severn Glocon stands ready to lead the way, setting new benchmarks for performance, reliability, and efficiency in valve technology.