Unveiling the role of Severn’s OCT TOV Butterfly Valve in cavitation mitigation and valve protection.
Severn understands the needs and demands of critical applications and for over 60 years have been pioneering technology development to solve industry needs and provide extended service life of our products. One of the significant issues we see with severe service application valves is cavitation.
Cavitation is only evident in fluid applications and the affects are well understood. However, challenges to offer the most cost-effective solution as opposed to the correct solution, can drive users to selecting sub optimal trims for the application. Users are often expected to understand all the implications of every application(s) to ensure the best valves are selected. At Severn, our industry experts use that knowledge to ensure the best technical solution is offered every time.
Cavitation is a phenomenon that is often seen in valve applications. This can cause dangerous and costly problems to the end user as it only occurs in liquid applications and usually when the flow is being throttled. When cavitation occurs it often creates severe levels of noise and vibration that not only is hazardous to the user but can also cause considerable damage, resulting in costly and unplanned downtime and maintenance. At Severn, we have seen first-hand the effects of cavitation on trims, reducing valve lifetime from years to just weeks, through our ‘Repair Intelligence.’
Cavitation occurs when the fluid in a valve reduces in pressure to a point at which the pressure is below the vapour pressure of the fluid. But what does this mean? If we consider water boiling this is an example of the vapour pressure of a fluid being reached at atmospheric pressure. If we now put the water in a vacuum, then we can make the same fluid boil at a reduced temperature. These pressures and temperatures at which the fluid vapour pressure sits are specific to each fluid type and as such each case must be treated independently.
When a fluid passes through an orifice such as a valve or trim, we see the pressure is inversely proportional to the velocity of the fluid. As the velocity increases through the valve the pressure will decrease.
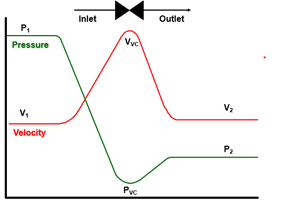
This can, in some circumstances, cause the pressure to fall below that of the vapour pressure of the fluid.
In this instance bubbles will occur in the fluid. When this happens the volume of the fluid can increase but the space inside the valve does not. This leads to the potential of increased velocity through the valve. Should there be entrained solids (such as sand) within the valve then this can have a significant erosion effect on the valve and be a cause for premature wear.
After the fluid has passed through the restriction it recovers in pressure on the other side of the orifice. This recovery in pressure and associated reduction in velocity can cause the fluid to recover above the vapour pressure of the fluid.
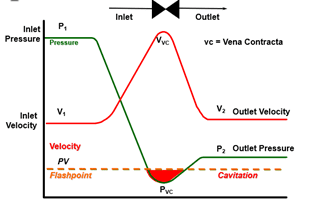
This causes the bubbles previously formed to rapidly collapse producing a shockwave. The forces involved in this are extremely violent. So much so the implosions can tear metal from components creating the characteristic pitting seen with cavitation failure.
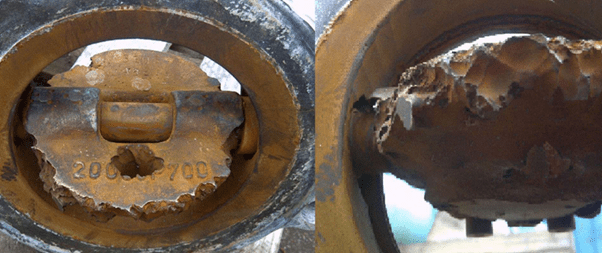
Aside from the physical damage to the valve internals, cavitation can manifest itself as loud noises, often described as “marbles in the pipeline.” These soundwaves create significant vibrations in the valves, pipework, and instrumentation, leading to failures of equipment outside of the valves flow paths due to high vibration and fatigue.
How does Severn’s OCT TOV Butterfly Valve mitigate the effects of cavitation?
By controlling the pressure drop through the valve we can prevent the onset of harmful cavitation. In a Butterfly Valve this often occurs at low openings. At these low openings we often see high velocities between the disc and valve body. Severns patented Oblique Cone Technology (OCT) allows the use of a fully circular disc and with the benefit of a true circle comes the advantage that full anti-cavitation / low noise trims can be fitted where required providing excellent cavitation control whilst still providing reliable shutoff.
In combination with the anti-cavitation disc, the OCT TOV Butterfly Valve can also be fitted with a full or half baffle as required to offer the best solution dependent on the process conditions provided.
At Severn, it is critical that the application knowledge is applied to the valve sizing to ensure the best possible solutions for the end user, ensuring costly unplanned downtime is kept to a minimum whilst achieving safe operations.
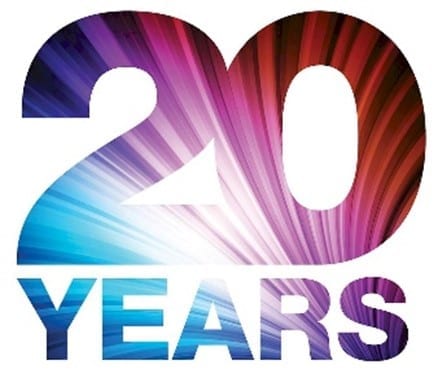
Severn celebrating 20 years with Shell.
Back in 2000 Severn Unival secured a valve management contract for Shell’s North Sea platforms. Each time the contract has come up for renewal we have retained the business. The contract was recently renewed again, marking 20 years of working together. The strength and duration of this customer relationship are testament to the high level of service and technical expertise we bring and is a major factor in Severn celebrating 20 years with Shell.
Severn manufactures and supports high quality valves for the energy industries. Its control, choke and small bore subsea valves are pre-eminent in the global market, underpinning the reliability and high performance of business-critical client infrastructure.
Severn’s global reach, technical prowess, and collaborative approach – all founded upon a heritage of British engineering excellence – help to assure production continuity for clients and reduce the prospect of costly downtime.
Its understanding of the life-cycle of assets positions Severn to offer end-to-end engineering solutions, enabling clients to meet their core imperatives: safe operations and minimum downtime.